Volume 2 - Year 2014 - Pages 52-58
DOI: 10.11159/ijepr.2014.008
CO2 Sequestration by Direct Dry Gas-Solid Contact of Serpentinite Mining Residues: A Solution for Industrial CO2 Emission
Sanoopkumar Puthiya Veetil¹*, Guy Mercier¹, Jean Francois Blais¹, Emmanuelle Cecchi¹, Sandra Kentish²
¹INRS-ETE 490 rue de la couronne, Québec, Canada
sanoopkumar.puthiya_veetil@ete.inrs.ca; guy.mercier@ete.inrs.ca
²The University of Melbourne,
Chemical and Biomolecular Engineering, VIC 3010, Australia
sandraek@unimelb.edu.au
Abstract - Direct dry gas-solid carbonation is a simple approach towards mineral carbon dioxide sequestration. The route theoretically implies the direct reaction of CO2 with silicates of Calcium and Magnesium in dry condition to form stable, insoluble metal carbonates. The mining regions of southern Québec have a large deposit of serpentinite residues. The current study examines the suitability of serpentinite mining residues to use as feedstock material for mineral carbonation. The focus of the present work is to assess the CO2 removal efficiency of the residue from a simulated flue gas mixture of a typical cement plant (18 Vol% CO2). This approach avoids the requirement of separate CO2 capture and pre-concentration prior to mineral carbonation. The reaction parameters considered are temperature, pressure and time. The optimization of parameters is carried out for the maximum CO2 removal efficiency (%) from the feed gas. Operating condition for CO2 removal is optimized at 258 °C, 5.6 barg (pCO2 ≈ 1) for 310 minutes with a removal efficiency of 37%. Preliminary analysis of reacted solid indicates carbonation is null at optimum condition, possibly a reversible adsorption might be responsible for the depletion of CO2 from feed gas. The study also checks the importance of pre-treatment options such as grinding, magnetic separation and heat treatment on CO2 removal. A separate optimization study is carried out for magnetic separation of serpentinite residue and the separation parameters are optimized at an initial pulp density of 40% and magnetic intensity of 7.5*10-3 T with about 70% of iron oxide removal from the initial feed.
Keywords: Serpentinite, mining residues, CO2 sequestration, direct dry gas-solid
© Copyright 2014 Authors - This is an Open Access article published under the Creative Commons Attribution License terms. Unrestricted use, distribution, and reproduction in any medium are permitted, provided the original work is properly cited.
Date Received: 2013-02-27
Date Accepted: 2014-04-02
Date Published: 2014-05-30
1. Introduction
The augmentation of greenhouse gases such as carbon dioxide (CO2) in the atmosphere has led to an increase in global temperature and changes in the climate. In order to mitigate the potentially devastating consequences of that phenomenon, the emissions of anthropogenic greenhouse gases especially CO2 into the atmosphere should be reduced [1]. Carbon dioxide capture and storage (CCS) is a well-known option for mitigating the unwanted anthropogenic CO2 emissions. Geological formation and ocean are the widely used sinks for carbon dioxide storage, but they are limited either due to the lack of permanence in storage or due to environmental issues associated with storage [2]. Mineral carbonation is the promising CCS option which guarantees the permanent storage of CO2 sequestrated [3, 4]. This option mimics the process of natural silicate weathering in which CO2 reacts with the divalent cation (Ca2+ or Mg2+) of natural minerals to form metal carbonates [5]. The carbonates formed are environmentally benign and geologically stable [2-4, 6]. Mineral carbonation is now in the developing stage, but the cost and kinetics keep it laid-back from other CO2 storage options [2]. Mafic and ultramafic rocks containing magnesium (Mg) and calcium (Ca) are generally used for mineral carbonation due to their relative abundance and admissible reactivity with CO2 [5]. In comparison to other metal silicates, magnesium based minerals such as serpentine and olivine are most abundant in nature [7]. Therefore, these minerals are under research scrutiny to develop as a cheap raw material for mineral carbonation [8, 9]. Besides these natural forms, waste materials contained admissible concentration of Mg and Ca have also been employed as mineral carbonation feedstock. These include mineral tailings of asbestos, industrial waste like stainless steel slag, waste cement, fly and bottom ash from municipal solid waste incinerator etc. [1, 7].
Mineral carbonation could be done either directly or indirectly through aqueous or dry route. Direct gas-solid route is a straight forward approach towards mineral carbonation and exothermic in nature [7, 10, 11]. Since the carbonation rate of pure mineral under direct dry condition was found to be slow, many modifications were recently suggested. Most recent works have been reported using a multistep gas-solid carbonation of magnesium hydroxide [Mg(OH)2] produced from serpentine [12-16]. Another recent approach has been reported with the addition of a small amount of water or water vapor for carbonation enhancement [17-21]. Most of the previous works on direct gas-solid route was mainly focused on the carbonation of solid material [13, 19, 21, 22] and less work have been reported on the CO2 depletion potential of minerals [18, 20].
The present is a preliminary laboratory study conducted using a batch wise mode. The objective of the study is to check the feasibility of serpentinite mining residue as a CO2 removal or carbonation material using direct dry gas-solid route. The mining residue used is from a chrysotile extraction mine in southern Québec. Direct dry gas-solid route was selected because of the simplicity and exclusion of chemical additives. The study adapted a new strategy of directly using a readily available mining residue for the capture and storage of CO2 from an industrial flue gas. Instead of pure mineral, using a mine residue that contains various mineral phases might provide a better reaction and could avoid the mining and mineral purification requirements. Direct use of a flue gas composition (18% CO2) could avoid the separate steps of CO2 capture and pre-concentration.
2. Experimental Section
Serpentinite Mining Residue (SMR) collected from Black Lake mine (Québec) was used for the present study. Collected samples were homogenised and then stored in separate sealed containers. The moisture content of the raw sample was measured by heating the mineral sample at 110 °C for around 24 h. The texture analysis of the sample was carried out by sieving through meshes with different cut sizes between 0.075 mm to 2 mm.
2.1. Material Characterization
Mineral phase of the residue was identified by X-ray diffraction (XRD) analysis using a Siemens D5000 diffractometer with Cu Kα radiation. Scans were taken for 2θ over 2° to 65° at 0.02°/s. Microscopic imaging and a semiquantitative analysis of the sample was done with a scanning electron microscope (SEM) equipped with energy dispersive X-ray spectroscopy (EDS) (Zeiss Evo 50 Smart SEM). Chemical composition of the mineral sample was determined by inductively coupled plasma atomic emission spectroscopy (ICP-AES) (Varian 725-ES, Model Vista-AX CCO, Palto Alto, CA, USA) after an alkaline fusion with lithium metaborate. The specific surface area and average pore diameter of the sample were determined by means of Brunauer–Emmett–Teller (BET) analyzer (BELSORP-max, BEL Japan Inc). For this, the samples were dried and analyzed for N2 sorption and desorption isotherm at 77 K after degassing at >150 °C overnight and the residual pressure down to 10−5 Torr.
2.2. Experimental Procedure
2.2.1. Mineral Pre-treatment
The grinding of SMR was done in a shatter-box (BLEULER-NAEF shatter-box, model M04/06) to increase the surface area and thereby enhance the reaction rate. The particle size of the ground SMR was determined by a laser particle analyzer (Horiba laser particle size distribution analyzer LA-950). The others pre-treatments options adapted for the current study were thermal heat treatment and magnetic separation. Temperature for thermal treatment was adapted from the previous studies conducted with similar type materials [23-27]. For this, the ground SMR was heated to 650 °C for 30 min in an air muffle furnace (Thermolyne Furnatrol 133). Magnetic separation was carried out by using a wet high intensity magnetic separator(WHIMS -CARPCO model serial no. 221-02) in order to remove the magnetic impurities; especially compounds of iron (Fe) from SMR. This was carried out to avoid the formation of a passive layer of iron oxide such as hematite during heat treatment which negatively affects the carbonation process [27, 28]. Conducting magnetic separation prior mineral carbonation can also provide final carbonation products of less magnetic impurities and a separate stream of magnetic by-product with good potential market value. Optimization of parameters for magnetic separation of SMR was separately carried out and the non-magnetic sample at optimum condition was used for direct dry gas-solid experiments. Parameters considered for the magnetic separation study were magnetic intensity (T) and initial pulp density (%).
2.2.2. Direct Dry Gas-solid Reactio
Samples for direct dry mineral reaction were categorized into three types: (1) raw, (2) heat-treated, and (3) magnetically separated samples. All tests were conducted in a batch reactor designed by Parr (Parr 4560 Mini Bench Top Reactor) of capacity 300 mL. The representation of the experimental set-up is given in Figure 1.
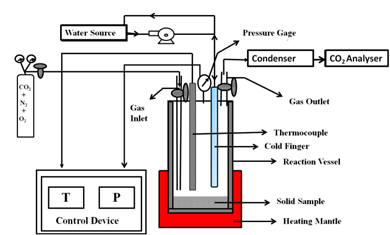
Direct dry gas-solid reactions were carried out by contacting ground SMR with CO2 gas mixture (N2/CO2/O2-78/18/4% (v/v)) at varying temperature and pressure. Based on the previous studies on this route, the reaction parameters considered for optimization were temperature, pressure and time [11, 12, 19, 29]. The direct dry gas-solid experiments were conducted by loading a definite mass (g) of ground SMR into the reactor. Then, it was heated to the desired reaction temperature (°C). After reaching the reaction temperature, the air and moisture inside the reaction vessel was purged and filled with the gas mixture to a desired pressure (bar). After a certain reaction time (min), the non-reacted gas was collected in a Tedlar Bags (3.8 L) equipped with an on / off valve and subjected to analysis. The concentration of CO2 (Vol%), before and after reaction, was measured by means of a CO2 analyzer (Quantec instrument model 906) and the mass of CO2 in the inlet and outlet gas was calculated using the ideal gas equation (PV=nRT) by knowing the reaction temperature and CO2 partial pressure.
The reaction deciding factor considered in the parameters optimization was the efficiency of CO2 removal (%) (Equation 1). Initial experiments were conducted in conventional method (single variable at a time) using raw, heat-treated and nonmagnetic sample. This was carried out to get an approximate idea about the parameter influence on CO2 removal. Then, the optimization was carried out with a statistical Box-Behnken model (Design Expert with ANOVA: Version 8.0.4, Stat-Ease Inc., Minneapolis, USA). The independent variables considered for the model were temperature, total pressure and time with corresponding ranges of 25 to 280 °C, 5 to 95 bar and 120 to 360 min respectively. The model designed 17 experiments and heat-treated sample of 25 g was used for the each experiment. Based on the experimental results obtained, the model predicted a most desirable interaction of parameters for the maximum response. Experimental validation of the model was carried out on the predicted optimized conditions. Comparative results were also generated with raw and nonmagnetic sample at optimum conditions.
CO2 removal efficiency (%) = ((CO2in– CO2out)/ CO2out) x 100 |
(1) |
Where CO2 in is the mass of CO2 in the inlet gas and CO2 out is the mass of CO2 in the outlet gas. The solid samples at optimum result conditions were subjected to both elemental carbon analysis (Leco CHNS-932 auto analyzer) and XRD to assess the formation of carbonates.
3. Results and Discussion
3.1. Characterization of SMR
The average interstitial water content of SMR from Black Lake residue was about 5.3% (±0.5). The texture analysis of SMR shows about 38% of the sample was above 2 mm, 22.9% was between 1 to 2 mm and remaining 39.1% was below 1 mm. Since 60% of the sample was above 1 mm, grinding was adapted to reduce the size to a micro level. The mean size of the ground SMR given by laser particle analyzer was 75 µm with 90% distribution below 250 µm. The XRD gives major peaks for lizardite associated with minor components such as chrysotile, magnetite, brucite, talc and chlorite. This is in concurrence with mineral compositions reported for similar type materials near the present sampling station [17, 26, 30, 31]. The EDS analysis of the site within the SEM images confirmed the presence of Fe substituted lizardite and magnetite (Fe3O4). The chemical composition of SMR in each size fraction is presented in Table 1. The sample is mainly concentrated with magnesium and silicon with a considerable level of Fe. This confirms the presence of serpentine group mineral (lizardite). The presence of Fe would account for both magnetite and partial substituted Fe within the lizardite structure. The average percentage of MgO (42.5±0.2%) and SiO2 (40±0.4%) in SMR are admissible range with known average value for lizardite [32]. The BET specific surface area and average pore diameter of the SMR were 11.5 m2/g and 13.7 nm respectively.
Table 1. Particle size distribution and chemical composition of SMR from Black Lake mine.
Mesh size |
Weight |
Fe2O3 |
MgO |
SiO2 |
Ni |
Co |
Cr |
≥2 |
38.0 |
11.1 |
41.5 |
37.0 |
2409 |
63.9 |
2493 |
1-2 |
22.9 |
9.0 |
36.9 |
37.7 |
1702 |
107.6 |
2010 |
0.5-1 |
17.8 |
10.1 |
41.3 |
37.9 |
2017 |
74.8 |
2160 |
0.3-0.5 |
9.3 |
11.9 |
39.4 |
36.5 |
1895 |
63.3 |
1991 |
0.15-0.3 |
7.5 |
12.2 |
34.8 |
35.9 |
1696 |
108.6 |
2554 |
0.075-0.15 |
3.4 |
18.6 |
36.9 |
34.5 |
1968 |
73.4 |
2856 |
≤0.075 |
1.1 |
21.9 |
31.9 |
32.4 |
1739 |
135.3 |
2545 |
3.2. Magnetic Separation
The best conditions for magnetic separation of SMR from mine Black Lake was optimized at a magnetic intensity of 7.5*10-3 T and an initial pulp density of 40% with ground SMR of mean size 75 µm. The second pass of magnetic separation products at above mentioned conditions given a maximum non-magnetic mass recovery of 90.0% (±0.2). The magnetic separation reduces the iron oxide (as Fe2O3) concentration of SMR from 10.9% (±0.4) to 3.4% (±0.1). From the raw feed about 97% of magnesium has been recovered in non-magnetic fractions. The final recovered magnetic fraction is rich in iron oxide with 79.0% (±0.3) composition. All the above results are calculated based on the ICP-AES analysis (after alkaline fusion with lithium metaborate). In short, conducting magnetic separation at above conditions resulted in 70% of iron oxide impurities removal from feed SMR.
3.3. Direct Dry Gas-solid Reaction
The maximum CO2 removal obtained using conventional single variable method was about 36.7% (±2) with heat treated sample at 200 °C, 5 bar (pCO2 =0.90 bar) after 360 min (6 h) duration. The response surface methodology (RSM) graph obtained from Box-Behnken analysis is given in Figure. 2. The result shows that the CO2 removal percentage was increased with increases in temperature and decreases in total pressure. The Model Prob > F value less than 0.05; implies that the model is significant. The value of multiple regression coefficients, R2 = 0.98, shows that the model could explain 98% of the response variability and which was in reasonable agreement with the adjusted R2 value (0.94). The model predicted an optimum condition at 258 °C, 5.6 bar (pCO2 ≈ 1) for 310 min (̴ 5 h) with 40% CO2 removal and was validated experimentally with 37% (±0.6) CO2 removal at these conditions. Direct dry reaction of raw and non-magnetic samples was also conducted at optimum condition (Box-Behnken) and obtained almost equal CO2 removal. At the maximum removal efficiency (37%), 25 g SMR removed about 0.12 g (±0.01) of CO2 from the feed gas with initial CO2 concentration of 0.32 g CO2. The elemental carbon and XRD analysis carried for reacted solid at optimum conditions did not show any variation from the original sample. This indicates CO2 might be removed from the feed gas due to a reversible adsorption rather than carbonation.
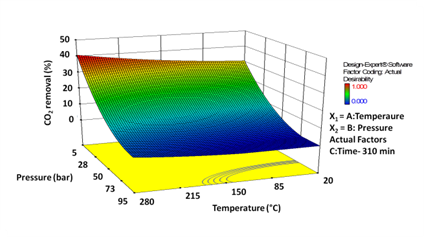
The results furnished for CO2 removal are only based on the CO2 analyzer measurement. The current removal is too low for practical application. We suggest that a limited CO2 removal occurred due to the poor gas-solid contact in the batch set-up. Experiments are required to be conducted with the presence of water vapor to enhance carbonation [17-21]. More process improvement is required to enhance the CO2 removal efficiency of solid such as increasing the gas-solid interaction through the fluidization of the bed and increasing the surface area and pore size of solid through a series of grinding.
4. Conclusion
The present work highlighted a new approach towards direct gas-solid carbonation by incorporating a mine waste for the direct capture or sequestration of CO2 from an industrial chimney. The usage of a residue rather than pure mineral can help in avoiding the mining and mineral purification cost requirement for mineral CO2 sequestration. Beside this, the process will revalorize the waste residue into environmentally benign material that can be used for land filling and mine reclamation (only if carbonation occurs). Switching from 100% CO2 to simulated flue gas composition of 18 Vol% CO2 can reduce the separate CO2 capture and pre-concentration cost. The main challenge of the route is achieving an admissible reaction rate with a low cost and energy consuming process.
The preliminary results obtained through the characterization and the parameter optimization for the mineral CO2 sequestration of SMR shows that SMR can be selected as a feedstock for CO2 sequestration. The reacted solid analysis indicates that the carbonation under dry condition is negligible, but that the CO2 is depleted from the feed gas possibly due to a reversible adsorption. Carbonation possibilities have to be assessed by the addition of water vapor. Studies are further required in a suitable design such as fluidized bed providing better gas-solid interaction to increase the reaction rate and kinetics. More extensive studies are required in this area to reach an admissible reaction rate and kinetics and thereby develop a promising process for an industrial application. The prime goal of the future work is to have an admissible carbonation reaction at low pressure and low temperature within the short reaction period.
Acknowledgements
The authors are grateful for financial support from the Fonds Québécois de la Recherche sur la Nature et les Technologies (FQRNT), Carbon Management Canada and the support from INRS-ETE, Quebec, Canada.
References
[1] IPCC, "Synthesis Report of the IPCC on climate change," Valencia, Spain, 2007. View Article
[2] IPCC, "IPCC special report on carbon dioxide capture and storage," Cambridge University Press, Cambridge, United Kingdom and New York, NY, USA, 2005. View Article
[3] W. Seifritz, "CO2 Disposal by mean of silicates," Nature, vol. 345, pp. 486-486, Jun 7 1990. View Article
[4] K. S. Lackner, C. H. Wendt, D. P. Butt, E. L. Joyce, and D. H. Sharp, "Carbon-dioxide disposal in carbonate minerals," Energy, vol. 20, pp. 1153-1170, Nov 1995. View Article
[5] W. J. J. Huijgen and R. N. J. Comans, "Carbon dioxide sequestration by mineral carbonation: Literature review," Energy Research Centre of the Netherlands, vol. ECN-C--03-016, 2003. View Article
[6] K. S. Lackner, "Climate change: A Guide to CO2 Sequestration," Science, vol. 300, pp. 1677-1678, 2003. View Article
[7] W. J. J. Huijgen and R. N. J. Comans, "Carbon dioxide sequestration by mineral carbonation: Literature review update 2003-2004," Petten, The Netherlands, ECN-C--05-0222005.
[8] H. Bearat, M. J. McKelvy, A. V. G. Chizmeshya, D. Gormley, R. Nunez, R. W. Carpenter, K. Squires and G.H. Wolf "Carbon sequestration via aqueous olivine mineral carbonation: Role of passivating layer formation," Environmental Science & Technology, vol. 40, pp. 4802-4808, Aug 1 2006. View Article
[9] M. J. McKelvy, A. V. G. Chizmeshya, J. Diefenbacher, H. Béarat, and G. Wolf, "Exploration of the Role of Heat Activation in Enhancing Serpentine Carbon Sequestration Reactions," Environmental Science & Technology, vol. 38, pp. 6897-6903, Dec 1 2004. View Article
[10] J. Sipilä, S. Teir, and R. Zevenhoven, "Carbon dioxide sequestration by mineral carbonation - Literature review update 2005-2007," Abo Akademi, 2008. View Article
[11] R. Zevenhoven, S. Teir, and S. Eloneva, "Heat optimisation of a staged gas-solid mineral carbonation process for long-term CO2 storage," Energy, vol. 33, pp. 362-370, Feb 2008. View Article
[12] J. Fagerlund, E. Nduagu, I. Romão, and R. Zevenhoven, "A stepwise process for carbon dioxide sequestration using magnesium silicates," Frontiers of Chemical Engineering in China, vol. 4, pp. 133-141, 2010. View Article
[13] J. Fagerlund, E. Nduagu, I. Romão, and R. Zevenhoven, "CO2 fixation using magnesium silicate minerals part 1: Process description and performance," Energy, vol. 41, pp. 184-191, 2012. View Article
[14] E. Nduagu, T. Björklöf, J. Fagerlund, J. Wärnå, H. Geerlings, and R. Zevenhoven, "Production of magnesium hydroxide from magnesium silicate for the purpose of CO2 mineralisation–Part 1: Application to Finnish serpentinite," Minerals Engineering, vol. 30, pp. 75-86, 2012. View Article
[15] R. Zevenhoven, J. Fagerlund, E. Nduagu, I. Romão, B. Jie, and J. Highfield, "Carbon Storage by Mineralisation (CSM): Serpentinite Rock Carbonation via Mg(OH)2 Reaction Intermediate Without CO2 Pre-separation," Energy Procedia, vol. 37, pp. 5945-5954, 2013. View Article
[16] J. Fagerlund, E. Nduagu, and R. Zevenhoven, "Recent developments in the carbonation of serpentinite derived Mg(OH)2 using a pressurized fluidized bed," Energy Procedia, vol. 4, pp. 4993-5000, 2011. View Article
[17] J. Pronost, G. Beaudoin, J. Tremblay, F. Larachi, J. Duchesne, R. Hebert, M. Constantin, "Carbon Sequestration Kinetic and Storage Capacity of Ultramafic Mining Waste," Environmental Science & Technology, vol. 45, pp. 9413-9420, Nov 1 2011. View Article
[18] H. F. Da Costa, M. Fan, and A. T. R., "Method to sequester CO2 as mineral carbonate," U.S Patent, 20100221163A1, 2010. View Article
[19] F. Larachi, I. Daldoul, and G. Beaudoin, "Fixation of CO2 by chrysotile in low-pressure dry and moist carbonation: Ex-situ and in-situ characterizations," Geochimica Et Cosmochimica Acta, vol. 74, pp. 3051-3075, 2010. View Article
[20] S. Kwon, M. Fan, H. F. DaCosta, and A. G. Russell, "Factors affecting the direct mineralization of CO2 with olivine," Journal of Environmental Sciences, vol. 23, pp. 1233-1239, 2011. View Article
[21] F. Larachi, J. P. Gravel, B. P. A. Grandjean, and G. Beaudoin, "Role of steam, hydrogen and pretreatment in chrysotile gas–solid carbonation: Opportunities for pre-combustion CO2 capture," International Journal of Greenhouse Gas Control, vol. 6, pp. 69-76, 2012. View Article
[22] R. Zevenhoven, J. Kohlmann, and B. A. Mukherjee, "Direct Dry Mineral Carbonation for CO2 Emissions Reduction in Finland," in 27th International Technical Conference on Coal Utilization & Fuel Systems Clearwater (FL), USA, 2002. View Article
[23] M. M. Maroto-Valer, D. J. Fauth, M. E. Kuchta, Y. Zhang, and J. M. Andresen, "Activation of magnesium rich minerals as carbonation feedstock materials for CO2 sequestration," Fuel Processing Technology, vol. 86, pp. 1627-1645, Oct 2005. View Article
[24] G. W. Brindley, "A structural study of the thermal transformation of serpentine minerals to forsterite," American Mineralogist, vol. 42, pp. 461-474, 1957. View Article
[25] C. Jolicoeur and D. Duchesne, "Infrared and thermogravimetric studies of the thermal degradation of chrysotile asbestos fibres: evidence for matrix effects", Canadian Journal of Chemistry, v. 59, p. 1521-1526., 1981. View Article
[26] M. Nagamori, A. J. Plumpton, and R. Le Houillier, "Activation of magnesia in serpentine by calcination and the chemical utilization of asbestos tailings - a review," CIM Bulletin, vol. 73, pp. 144-156, 1980.
[27] W. O'Connor, D. Dahlin, G. Rush, S. Gerdemann, L. Penner, and D. Nilsen, "Aqueous mineral carbonation, mineral availability, pretreatment, reaction parametrics, and process studies," in US DOE, DOE/ARC-TR-04-002, Albany Research Centre: Albany, OR, 2005., 2004.
[28] W. K. O'Connor, D. C. Dahlin, D. N. Nilsen, R. P. Walters, and P. C. Turner, "Carbon dioxide sequestration by direct aqueous mineral carbonation," in Proceedings of the 25th International Technical Conference on Coal Utilization & Fuel Systems, Clear Water, Florida., 2000. View Article
[29] R. Baciocchi, A. Polettini, R. Pomi, V. Prigiobbe, V. N. Von Zedwitz, and A. Steinfeld, "CO2 sequestration by direct gas-solid carbonation of air pollution control (APC) residues," Energy & Fuels, vol. 20, pp. 1933-1940, Sep 20 2006. View Article
[30] I. M. Power, S. A. Wilson, D. P. Small, G. M. Dipple, W. Wan, and G. Southam, "Microbially Mediated Mineral Carbonation: Roles of Phototrophy and Heterotrophy," Environmental Science & Technology, vol. 45, pp. 9061-9068, 2011. View Article
[31] A. L. Auzende, I. Daniel, B. Reynard, C. Lemaire, and F. Guyot, "High-pressure behaviour of serpentine minerals: a Raman spectroscopic study," Physics and Chemistry of Minerals, vol. 31, pp. 269-277, Jun 2004. View Article
[32] A to Z Listing of Minearls, [Online] consulted 25 Feb. 2013. View Website