Volume 11 - Year 2023 - Pages 32-42
DOI: 10.11159/ijepr.2023.004
Treatment of Factory Effluent Using a Combined Co-agulation and Filtration System: Empirical Insights from Uganda
Gloria Linda Ndagire 1, Roice Bwambale Kalengyo2
1
Uganda Christian University
Kampala, Uganda
linda.ndagire@zadecadacademy.com
2 Ndejje university
Kampala, Uganda
Abstract - The treatment of wastewater from various sources, such as agricultural and industrial facilities, poses significant chal-lenges in improving public health and well-being, especially in developing countries like Uganda. This study aimed to address this issue by investigating the quality and quantity of wastewater from a specific factory in Uganda and design-ing a treatment system capable of meeting discharge stand-ards. The research involved sampling the wastewater at the factory and conducting both on-site and laboratory tests to assess its characteristics. The proposed treatment system consists of a mixing unit, sedimentation tank, and filtration unit. Coagulation/flocculation with alum was used in the mixing unit, followed by sedimentation to facilitate the set-tling of solids. In the filtration unit, commercial granular activated carbon was employed to adsorb contaminants, while sand was placed below it to capture remaining sus-pended solids after sedimentation. The results indicate that the combination of coagulation/flocculation and filtration processes effectively treats paint wastewater. The study ex-amined the system's performance at various effluent quali-ties by varying the initial contaminant concentrations. For initial contaminant concentrations of Chemical Oxygen Demand (COD) at 6,200 mg/L, Biological Oxygen Demand (BOD) at 489 mg/L, color at 39,000 mg/L, Total Phosphorus at 2,453 mg/L, and Total Nitrogen (TN) at 1,800 mg/L, the system achieved impressive removal efficiencies: 98.6% for COD, 91.4% for BOD, 99.6% for color, 99.2% for TN, and 99.8% for total phosphorus. In summary, this research paper presents a study on the treatment of paint wastewater from a factory in Uganda. The proposed treatment system, using coagulation/flocculation and filtration, demonstrates high removal efficiencies for various contaminants, making it a promising solution for addressing wastewater treatment challenges in the region.
Keywords: Paint wastewater treatment, wastewater characteristics, flow rate, sedimentation tank, filtration unit, integrated system
© Copyright 2023 Authors - This is an Open Access article published under the Creative Commons Attribution License terms. Unrestricted use, distribution, and reproduction in any medium are permitted, provided the original work is properly cited.
Date Received: 2023-07-17
Date Revised: 2023-08-21
Date Accepted: 2023-11-20
Date Published: 2023-12-12
1. Introduction
When used for decorative or protective purposes on various surfaces, paint is a liquid solution containing different pigments and solvents [1]. Paint can be catego-rized into oil-based and water-based varieties, utilizing oil and water as solvents, respectively.
Paint wastewater is known to contain hazardous compounds that can inhibit bacterial growth [2]. The improper disposal of paint and its wastewater poses a significant environmental concern, leading to toxic waste and potential health hazards. This issue is particu-larly critical in Kampala City, where surface and groundwater pollution pose serious risks of waterborne diseases to the city's inhabitants. A recent outbreak of typhoid was partly attributed to polluted water sources [3]. Addressing these challenges requires effective wastewater management and treatment to safeguard public health and the environment.
As a developing country experiencing a surge in in-frastructure construction, Uganda's demand for architec-tural paints is on the rise, leading to the establishment of new paint manufacturing industries and economic op-portunities [4]. However, this growth also increases the risk of paint wastewater contamination, necessitating measures to prevent environmental damage and health risks.
Globally, paint manufacturing industries are subject to stringent regulations, with many countries setting minimum standards for effluent disposal to prevent en-vironmental pollution. Consequently, paint manufactur-ers have been adopting low-solvent and solventless technologies over the past four decades, a trend likely to continue in the future [5]. These regulations are in place due to the significant environmental threat posed by paint wastewater.
This research paper contributes to the scientific knowledge of wastewater management and treatment, which plays a crucial role in promoting public health, livelihoods, and overall well-being. Additionally, it sup-ports environmental conservation and the protection of underwater biodiversity, aligning with the key demands presented at the 15th Conference of Parties (COP 15)
The paper is based on findings from a case study of a water-based paint factory in Kampala City, Uganda, and was guided by the following specific objectives.
- Determining the characteristics of the wastewater and the volume of wastewater gen-erated.
- Designing a treatment system for the wastewater from the case study factory.
- Examining the performance of the designed inte-grated treatment system in eliminating specific water contaminants.
1.1 Problem statement
The factory had an inefficient wastewater treatment system, resulting in the discharge of untreated wastewater into an underground pit and on land (shown in Fig. 1). According to Part 5(1) of the National Envi-ronment Regulation for Discharge of Effluent into water or onto land, all industries are required to have a treat-ment facility and regulate the amount of waste generat-ed to meet environmental standards [6]. The current management of the factory's wastewater presents a sig-nificant risk of leakage into the surrounding environ-ment, including water channels and downstream streams that people rely on [7].
The high levels of pollutants in water channels, such as Biological Oxygen Demand (BOD), Chemical Oxygen Demand (COD), Total Suspended Solids (TSS), and Total Dissolved Solids (TDS), make the water unsuitable for drinking, home use, irrigation, and aquatic life. This neg-atively affects people's health and livelihood, as they become more susceptible to diseases. In addition, the runoff from paint wastewater can lead to the slow breakdown of organic solvents and inorganic com-pounds in water, depriving aquatic organisms of the ox-ygen they need to survive. These toxic chemicals can also cause tumours to form in animals such as fish.
About 35% of the world's population depends on shallow aquifers for their water needs [8], exposing them to the poisonous pollutants in the factory's wastewater. Moreover, some of the waste components may infiltrate and percolate into the subsurface envi-ronment upon discharge, accumulating in the soil pores [9]. Surface and groundwater quality has been declining due to industrialization and human activities [10].
This study aimed to design a treatment system for the factory by conducting wastewater sampling, field and laboratory tests, analysis, and design.
1.2 Justification of the problem
The wastewater generated by the paint factory is not disposed of properly, as it lacks an efficient effluent disposal management system. Instead, the factory uses an underground pit which is not sustainable and can have negative effects on soil productivity and concentra-tions [11], thereby posing risks to plant life in the long run. Moreover, these pits cannot effectively remove in-organic waste; nitrogen and phosphorus compounds that could lead to algal blooms in waterways in case of leakages [12].
Despite the existence of regulatory bodies such as the National Environment Management Authority (NE-MA) tasked with ensuring proper wastewater disposal, the paint factory does not conform to these regulations for effluent discharge.
There is a need for an appropriate wastewater treatment design to be implemented to ensure the prop-er treatment of effluent before discharge. This will re-duce the risk of contamination of underground water and land, protecting both human and plant life. Moreo-ver, implementing an appropriate wastewater treatment design will be a crucial step in achieving the UN Sustain-able Development Goals (SDGs), particularly Goal 14: Life underwater.
2. Methodology
This chapter outlines the methodology that was used to achieve the first specific objective. Sampling of the wastewater was carried out through field and labor-atory tests. Field tests were carried out at the case study factory and the laboratory tests at the National Water and Sewerage Corporate (NWSC)-Central Laboratory (Kampala, Uganda).
2.1 Field tests
Field tests were carried out for some of the wastewater parameters to determine its characteristics and flow rate to determine the quantity of wastewater generated.
2.1.1 Flow Rate measurements
The flow of wastewater fluctuated based on the day, week, or month. Wastewater was mainly produced dur-ing the evening, specifically during floor and mixing tank cleaning, resulting in elevated wastewater volumes dur-ing this time. To determine the flow rate at the wastewater outlet from the factory, the bucket method was employed (refer to Figure 2). The bucket method was chosen over other methods because it is appropri-ate for small flows and irregular channels.
2.1.2 Wastewater Characteristics
The wastewater characteristics were analyzed through field and laboratory measurements. Preliminary tests were performed by collecting wastewater samples at two sampling points. The first sampling point was lo-cated at the factory's wastewater outlet before the screening, and the second sampling point was in the un-derground pit after the screening. Screening is relevant in removing large, solid materials from the incoming wastewater before it undergoes further treatment. Therefore, the wastewater was screened before being directed to the underground pit to reduce the number of suspended solids.
To determine some of the wastewater characteris-tics such as temperature and dissolved oxygen, field tests were conducted. The Mettler Toledo and a DO MRC were used by a technician to measure the above parame-ters. Each of the above parameters was measured in trip-licate at both sampling points.
2.2 Laboratory Tests
The collected samples from the field were examined for various parameters, including colour, BOD, COD, TSS, TN, total phosphorus, alkalinity, cadmium and sulphate. The purpose of these tests was to assess if the wastewater parameters complied with the standards set by the National Environmental Management Authority (NEMA) for effluent discharge into the environment.
In addition to the tests, the jar test was performed to identify the optimal coagulant dosage needed to purify the wastewater.
3. Results and Discussion
After carrying out field and laboratory tests, the fol-lowing results were obtained, represented and inter-preted as shown below.
3.1.1 Wastewater quality characteristics
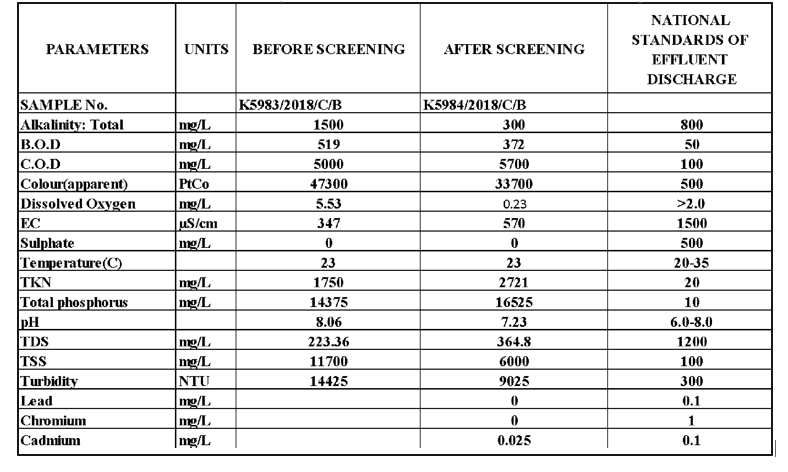
This study found that the levels of BOD, COD, Colour, Total Phosphorus, TKN, TSS, and Turbidity in wastewater were higher than effluent discharge stand-ards both before and after the screening. The high levels of BOD and COD were attributed to the use of various organic materials such as titanium dioxide, calcium car-bonate, magnesium silicate, and cellulose in the manu-facture of paint [13]. The colour was due to the presence of dissolved organic material, which also contributed to the high turbidity values [14].
The alkalinity and pH of the wastewater were also above the discharge standards before the screening, but within the acceptable range after the screening. This was because the wastewater still contained paint before the screening, whereas after the screening, some paint was removed by the screen, resulting in a lower pH.
The COD levels were high after screening because during the screening process, certain chemical reactions might occur, leading to the formation of new compounds or by-products that contribute to COD. Similarly some nitrogen and phosphorus compounds might dissolve or become more soluble during the screening process, leading to higher concentrations in the wastewater.
The study found that water-based paints, which use water as a solvent, had lower levels of heavy metals, as sulphate, lead, and chromium were not detected in the wastewater.
Finally, the study found that the dissolved oxygen (DO) levels were within the discharge range before the screening but out of range after the screening. This was due to the underground pit storage of the wastewater, which limited oxygen supply [15], thereby posing a threat to aquatic life and contributing to offensive odours. Adequate levels of dissolved oxygen are essen-tial for the survival of aquatic life and odour control.
3.1.2 Statistical analysis
Table 2: Error analysis for the influent
Parameters |
S.D |
UNITS |
Value |
||
Alkalinity: Total |
4.8 |
(mg/L) |
765.3±3.7 |
||
B.O.D |
1.2 |
(mg/L) |
487.03.7±2 |
||
C.O.D (mg/L) |
.1 |
(PtCo) |
6196.6±3.3 |
||
Colour (apparent) |
5.1 |
(S/m) |
39006.6±6.7 |
||
Electric Conductivity |
0 |
(°C) |
464.3±2.2 |
||
Temperature |
0 |
(mg/L) |
20.4±0.2 |
||
Total Nitrogen |
0 |
1796.6±3.3 |
|||
Total Phosphorus |
0 |
(mg/L) |
2453.3±3.7 |
||
pH |
0 |
(mg/L) |
7.15±0 |
||
Total Dissolved Solids |
0 |
295.5±.3.3 |
|||
Total Suspended Solids |
0 |
(mg/L) |
7288.3±7.2 |
||
Turbidity |
0 |
(NTU) |
9926.6±1.7 |
The percentage error is very high for most of the pa-rameters.
The influent values varied a little high for some pa-rameters like the Alkalinity since the results were given by the industry’s laboratory technologist thus less relia-bility of analysis could have triggered this kind of out-come.
Despite these limitations, the error analysis was useful tool for identifying areas where the data collec-tion policies of Uganda can be improved so that a better water quality assessment for industries is wholesomely analysed without restriction on some parameters.
Table 3: Error analysis for the effluent
Parameters |
UNITS |
Value |
S.D |
Alkalinity: |
(mg/L) |
236±2.8 |
4.8 |
B.O.D |
(mg/L) |
40.3±0.7 |
1.2 |
C.O.D |
(PtCo) |
92±1.2 |
2.1 |
Colour |
(S/m) |
125.3±2.9 |
5.1 |
Electric Conductivity |
(°C) |
523±0 |
0 |
Temperature |
(mg/L) |
20.2±0 |
0 |
Total Nitrogen |
|
14±0 |
0 |
Total Phosphorus |
(mg/L) |
2.61±0±0±0 |
0 |
pH |
(mg/L) |
7.03±0 |
0 |
Total Dissolved Solids |
|
334.7±0 |
0 |
Total Suspended Solids |
(mg/L) |
38±0 |
0 |
Turbidity |
(NTU) |
11.7±0 |
0 |
The reported value of alkalinity has a precision of ±2.8 mg/L, with a standard deviation of 4.8. The rela-tively large standard deviation suggests variability in measurements, which may be due to the nature of the water sample or the measurement technique. The re-ported value of BOD is precise to ±0.7 mg/L, with a standard deviation of 1.2. A low standard deviation indi-cates good precision. However, consider discussing the potential sources of variability and how they were con-trolled during the experiments. Precision is ±1.2 PtCo with a standard deviation of 2.1. Similar to alkalinity, the relatively large standard deviation suggests variability. The sources of variability are likely to be due to the mode of multiparameter meter equipment used, to be more precise next researches will ensure use of a most recent mode of equipment.
3.2 Wastewater flow rates from the case study Fac-tory
Below are the results obtained during the produc-tion days (weeks days) and the days when cleaning ac-tivities take place (Saturdays) for the month of February 2019.
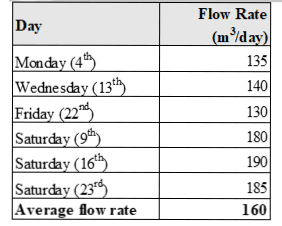
The production days had a flow rate between 130-140 m3/day while Saturdays had a flow rate between 180-190m3/day, as indicated in Table 2. The peak flow rates occurred on Saturdays during cleaning activities. There was no constant flow rate, so the average flow rate of 160m3/day was calculated to facilitate the appropriate design of the treatment system.
The flow rate measurements varied depending on the day and time due to the factory's batch process. Wastewater only flows mainly during production and cleaning activities, which occur at different times. Mon-day to Friday are typical production days with more paint production than cleaning. Therefore, the flow rate values are lower. Saturday is when the factory performs general cleaning, leading to more wastewater generation and peak flow rate values.
3.3 Determining the optimum dosage of alum.
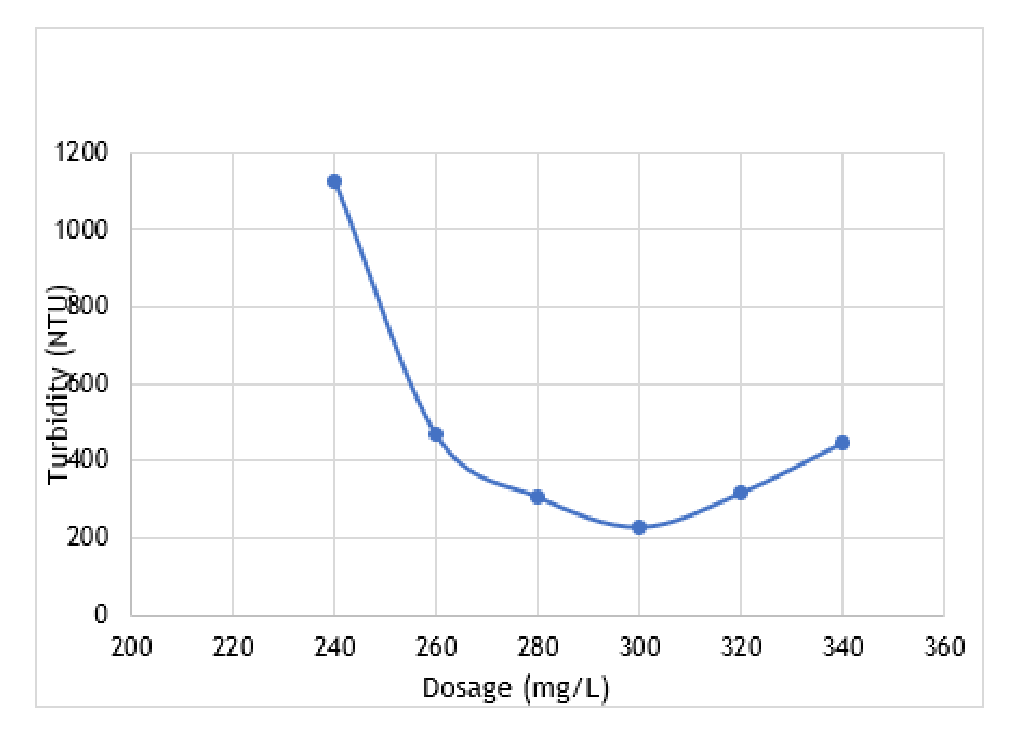
The research experiment conducted involved the measurement of turbidity and dosage of alum. Figure 3 displays the average values obtained from two jar tests with identical dosages, and the graph of turbidity against the dosage plotted based on the results. The data indi-cates that the optimal dosage of alum to achieve the lowest turbidity level is 300 mg/L, and this value was obtained at a pH of 7.68.
The pH of the wastewater was observed to increase between the range of 7.5-7.8 as the dosage of alum in-creased. This is attributed to the reaction between the different salts present in the paint manufacturing pro-cess, such as calcium carbonate and magnesium silicate, and alum. However, the pH did not exceed the neutral range of 7.8, and hence, no adjustments were necessary.
3.4 Design Prototype
The design of the wastewater treatment system was informed by the results obtained from tests. A prototype or laboratory scale design was established, and the wastewater was processed through the system, which is illustrated in Figure 4. Testing was conducted on the influent, coagulated wastewater, and effluent after filtra-tion. The efficiency of the system was evaluated based on the results.
The wastewater underwent several stages of treat-ment. Initially, it flowed from the mixing unit, where agi-tation of the wastewater and alum facilitated the coagu-lation-flocculation process. Next, the wastewater was directed to the sedimentation tank to allow the sus-pended solids to settle. Lastly, the wastewater was fil-tered through the filtration unit, where Commercial Granular Activated Carbon (GAC) adsorbed the contami-nants, and sand below. The placement of the GAC above the sand was advantageous because it has a large sur-face area for molecules to stick, facilitating the adsorp-tion process [16].
In addition, sand was placed below the GAC to cap-ture any remaining suspended solids and prevent the breakthrough of flocs [17]. To support the filter media, gravel was used as the base layer, following recommen-dations from [18].
3.5 Sampling of the design prototype
3.5.1 Influent and coagulated wastewater
Tests were carried out on the coagulated wastewater from the sedimentation tank and the results obtained are shown in the graph below. Coagula-tion/flocculation, and sedimentation effectively reduces the pollutants and allows slight improvement for wastewater characteristics. 90%, 69.3, and 74.3% of COD, BOD and colour removal efficiencies respectively. The results are attributed to the organic pollutants being soluble.
Despite the improvement in the wastewater charac-teristics for BOD, COD, Colour, TN, TP, TSS and Turbidity were still above the discharge standards of effluent. This is because paint wastewater can contain fine particles and colloidal suspensions that are difficult to settle through conventional coagulation and sedimentation. These particles remain in suspension, even after the co-agulation process. Therefore, a subsequent treatment was required to fully improve the wastewater character-istics and be within the discharge standards.
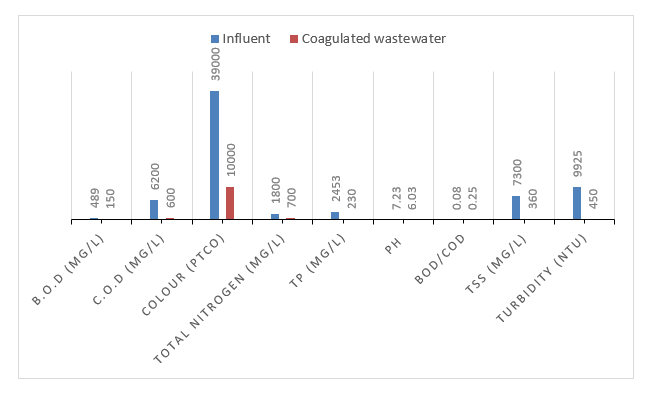
3.5.2 Influent and effluent
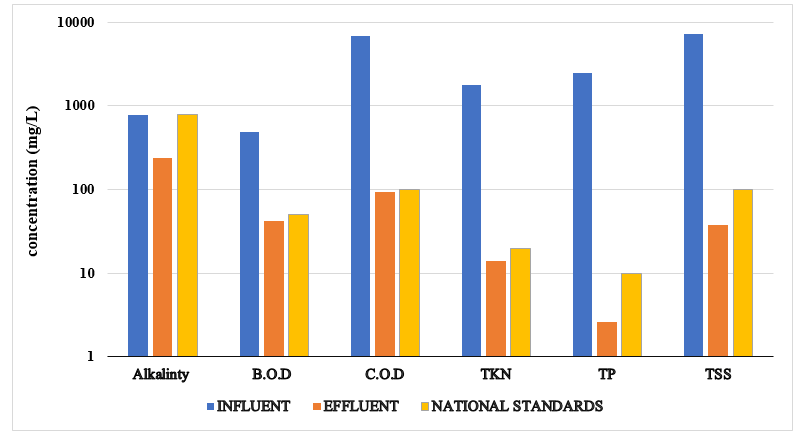
From the figure above, it is observed that the influ-ent parameters of BOD, COD, TP, TKN and TSS did not meet the required national discharge standards except for Alkalinity, DO and TDS which were within range.
After treatment the effluents parameters of BOD, COD, TKN, TP, TDS and TSS met the required discharge standards.
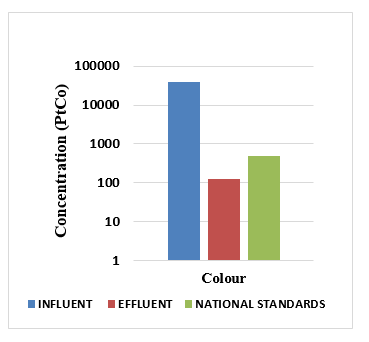
From the figure above, it is observed that Before treatment the colour was above the discharge standards. The turbidity reduced from 39,000 to 129PtCo after treatment and this was within the standards.
From the figure above, it is observed that Before treatment the turbidity was above the discharge stand-ards. The turbidity reduced from 9925 NTU to 11.7NTU after treatment and this was within the standards.
3.5.3 Percentage removal.
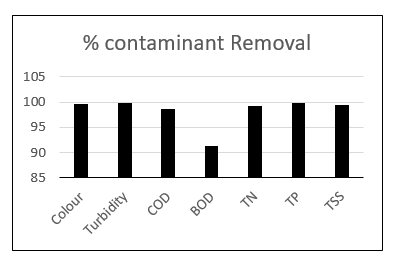
The efficiency of the wastewater treatment system was evaluated by calculating the percentage removal of the different parameters. The results showed that the system had a percentage removal of over 90% for all the parameters. These were within the discharge standards, indicating that the system was efficient in treating the wastewater from the Factory.
The sedimentation tank was utilized to settle solids, leading to a reduction in BOD and TSS. The tank enhanc-es the removal of approximately 50-70% of TSS and 25-40% of BOD, as supported by a study by [15]. The water was clearer after sedimentation, indicating a reduction in colour, turbidity, and BOD. The colour reduction was attributed to flocculation, which was a result of alum addition. The activated carbon in the system helped in the maximum removal of COD, TN, colour, and phospho-rus [19]. The filtering unit also helped in retaining sus-pended solids in the wastewater, further reducing the turbidity and BOD.
The proposed wastewater treatment system was compared to other designs used in treating water-based paints, such as the combination of a chemical coagula-tion-flocculation step with an aerobic biological process [20]. This system removed 92% of COD, 97% of colour, and 44.5% of BOD [20]. It was observed that the pro-posed system was more efficient than that of [20] espe-cially since it had a higher percentage of efficiency.
4. Final design of the treatment system adapted for large scale use.
4.1 Mixing Unit
The dimensions of the mixing unit were calculated in reference to Rapid mix design for mechanisms of Alum by Amirtharajah. A, and Kirk M in 2000.
Time of mixing alum and the wastewater = 5min
Q (flow rate) = 160m3/d = 0.11m/min
Diameter= 1m, radius= 0.5m
Height= 0.7m
4.2 Sedimentation tank
The design considered were in reference to Metcalf & Eddy, Wastewater Engineering: Treatment and Resource Recovery, vol. 4th Edition, New York: McGraw-Hill, 2003.
Flow rate=160m3/day
Detention time= 2h
Assumptions
Depth=1.5m,L=6W, Slope =1%,
Weir loading rate of 125m3/m2day
Tank specifications
Height= 1.5m
Length= 7.2m
Width= 1.2m
Settling velocity= 0.75m/hr
Surface loading = 18mm3/m2day
4.3 Filtration unit
The design considerations for the filtration unit were done in reference to the Environment Protection Agency, Water Treatment Manuals Filtration of 1995.
Prototype design
Flow rate = 160m3/d
Contact time= 10min
Filtration rate= 3,200m3/m2d
Column diameter = 250mm
Column height = 550mm
Bed depth (GAC)= 100mm
Bed depth (sand)= 100mm
Column dimensions
Diameter – 1.1m
Height – 2.5m
Bed depth (GAC)- 0.45m
Bed depth (sand)- 0.45m
Assumptions
Flow rate of the packed column=200cm3 /min
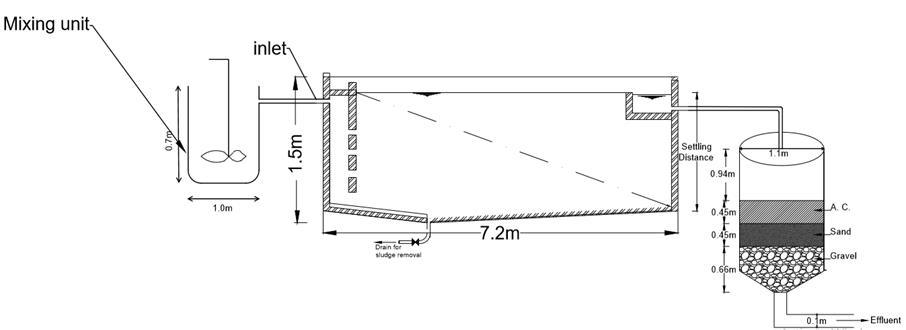
4.4 Working drawing of the treatment system adapted for large scale use.
From the above design considerations and calculations, drew the cross section and plan of the actual treatment system as shown below.
5. Conclusion
Compared to other existing designs used in treating water-based paints, such as [20] which removed 92% of COD, 97% of colour, and 44.5% of BOD. This integrated system has proven to be effective in treatment of paint wastewaters. It generates a clear effluent that is free of contaminants, with remarkable removal rates of above 90% for all the parameters.
Activated carbon has a 90% efficiency rate to absorb contaminants, and removes organics, bad taste, and odour. Sand filtration helps to remove suspended mat-ter. Coagulation and flocculation remove a large number of organic compounds as well as suspended particles.
All in all, the integrated system is more efficient in paint wastewater treatment, and generally simple to op-erate.
Urban development policymakers and implementers should work with engineers to promote and enforce sus-tainable paint wastewater management using such inte-grated systems.
Acknowledgment
I would like to express my deepest appreciation to the co-author (Roice Bwambale) for his valuable contri-butions to this research paper. He played a critical role in reviewing and editing this paper, providing construc-tive feedback and suggestions that significantly im-proved the clarity, coherence, and overall impact of the paper.
I would like to also express my heartfelt gratitude to my father for his unwavering support and encourage-ment throughout my research journey. Without his fi-nancial assistance, this research would not have been possible.
References
[1] R. Talbert, Paint Technology Handbook, New York: Taylor and Francis group, 2007. View Article
[2] K. Fent, "Ecotoxicology of organotin compounds," Critical Reviews in Toxicology, vol. 26, pp. 1-117, 1996. View Article
[3] Kampala City Council Authority, "Industrial Wastewater Management Guide for Paint Industries," Kampa-la, 2016.
[4] E. Adengo, "Daily Monitor," A battle of paints hits Uganda, p. 2, 20 September 2017.
[5] Chemical Economics Handbook, International guide to chemical engineering, ACS Publications, 2017.
[6] National Environment Management Authority, "Standards for Discharge of Effluent into Water or on Land in Uganda," Kampala, 1999.
[7] O. R. and O. O, "Preliminary Assessment of Effects of Paint Industry Effluents on Local Groundwater Re-gime in Ibadan, Nigeria," International Journal of Engineering Research, vol. 4, no. 10, pp. 518-522, 2015. View Article
[8] United Nations Environment Programme, "UNEP annual report for 2002," New York, 2002.
[9] R. Idzelis, K. Greičiūtė and D. Paliulis, "Investigation and evaluation of surface water pollution with heavy metals and oil products in kairiai military ground," Journal of Environmental Engineering and Landscape Management, vol. 14, pp. 183-190, 2006. View Article
[10] D. Kumar , S. Chadda, J. Sharma and P. Surain, "Syntheses, spectral characterization, and antimicrobial studies on the coordination compounds of metal ions with schiff base containing both aliphatic and aro-matic hydrazide moieties," 2013. View Article
[11] Y. Jolly, A. Islam, S. Quraishi and A. Mustafa, "Effects of Paint Industry Effluent on Soil Productivity," Jour-nal of Bangladesh Academy of Sciences, vol. 32, no. 1, pp. 41-53, 2008. View Article
[12] America Ground water trust, "Septic systems for wastewater disposal," USA, 2008.
[13] G. Kutluay, F. Germirli and G. Eremektar, "Treatability of water based paints," Fresenius Environmental Bulletin, vol. 13, pp. 1057-1060, 2004.
[14] F. El-Dars, M. Ibrahim and A. Gabr, "Reduction of COD in water-based paint wastewater using three types of activated carbon," Desalination and Water Treatment, vol. 52, pp. 16-18, 2014. View Article
[15] Metcalf & Eddy , Wastewater Engineering: Treatment and Resource Recovery, vol. 4th Edition, New York: McGraw-Hill, 2003.
[16] M. Sumrit , M. Phansiri , P. Wanwimon and K. Sataporn , "Characterization and Properties of Activated Carbon Prepared from Tamarind Seeds by KOH Activation for Fe(III) Adsorption from Aqueous Solution," The Scientific World Journal, vol. 2015, pp. Article ID 415961, 9 pages, 2015. View Article
[17] Environmental Protection Agency, Water Treatment Manual: Filtration, Johnstown Castle Estate, 2020.
[18] Ministry of Water and Environment, Water Supply Design Manual, Kampala: Second edition, 2013.
[19] T. Peta, Efficiency of activated carbon filters in COD reduction, 2006.
[20] M. Aboulhassan, S. Souabi, A. Yaacoubi and M. Baudu, "Treatment of paint manufacturing wastewater by combination of chemical and biological processes," International Journal of Science, Environment and Technology, vol. 3, no. 5, pp. 1747-1758, 2014.