Volume 11 - Year 2023 - Pages 20-31
DOI: 10.11159/ijepr.2023.003
Cradle-to-Gate Life Cycle Assessment of Cellulose-Based Membrane Manufacturing Process
Nasrin Attari 1,2, Robert Hausler1,2
1
École de Technologie Supérieure/ University of Quebec
2 La Station Expérimentale des Procédés Pilotes en Environnement (STEPPE-ÉTS)
1100 Notre-Dame St W, Montreal, Canada H3C 1K3
nasrin.attari.1@ens.etsmtl.ca
Abstract - Polymer nanocomposite membrane is an innovative and promising approach with a broad spectrum of potential applications in filtration processes. In spite of this, membrane production procedures are far from environmentally friendly and sustainable. A comprehensive understanding of its environmental impacts, covering the life cycle of the used materials and the fabrication process, is crucial for its long-term sustainable success. This research aims to elaborate and implement a decision-making tool for greener membrane fabrication process. The environmental impacts of synthesizing one batch of Nanocomposite cellulose nanofibrils/cellulose acetate membrane using 50 gr polymer dope solution by electrospinning technique was determined based on a life cycle assessment methodology. The eco-sufficiency and sustainability of the electrospinning method were evaluated through a cradle-to-gate life cycle assessment (LCA) adopting the Cumulative Energy Demand (CED), and IMPACT2002+ impact assessment methods. According to CED assessment, the majority of energy consumed during electrospun membrane synthesis, amounting to 382 MJ, was consumed by the production of cellulose nanofibers. This is related to non-renewable fossil energy consumed in Ethanol production. As per IMPACT2002+ impact assessment, cellulose acetate and cellulose nanofiber manufacturing, and medium voltage electricity are the main contributors to the overall midpoint environmental impacts. A number of hotspots in the membrane production process were identified, and measures were suggested for reducing the environmental impact of membrane production.
Keywords: Life Cycle Assessment, Electrospinning, Membrane Technology, Polymer Nanocomposite, Cellulose, Uncertainty Analysis.
© Copyright 2023 Authors - This is an Open Access article published under the Creative Commons Attribution License terms. Unrestricted use, distribution, and reproduction in any medium are permitted, provided the original work is properly cited.
Date Received: 2023-08-06
Date Revised: 2023-09-10
Date Accepted: 2023-09-26
Date Published: 2023-09-29
1. Introduction
It is expected Many advanced separation processes are made possible by membrane technology, which has found a wide range of applications in industry and in human life. Membrane technology is used in water treatment, wastewater treatment, food processing, drug delivery, biotechnology, and other industrial applications. It is also used in medical treatments such as dialysis and in the production of hydrogen fuel cells [1]–[3]. It is relatively inexpensive, environmentally friendly, and easy to process, which makes polymers the most popular membrane material in the industry [4]. Polymeric membranes offer advantages over traditional techniques such as distillation, adsorption, and absorption. In recent years, polymeric membranes have gained industrial attention because of their simplicity, cost-effectiveness, and small footprints [1], [5].
The electrospinning process is a simple, innovative, versatile, and a relatively low-cost way to produce nanofibers and nanocomposites with superior properties compared to conventional fibers, such as enhanced tensile strength, thermal stability, and chemical resistance [6]. A further advantage of electrospinning is its ability to create fibers with controllable diameters, higher porosity and surface to volume ratio which are desirable for water and wastewater treatment applications. Diameters of electrospun fibers usually range from 50 nm to 10 ㎛ [7]–[9]. It has been known that electrospinning mechanisms date back to the 19th century [10], but environmental effects associated with nanofibrous membrane fabrication are still under investigation.
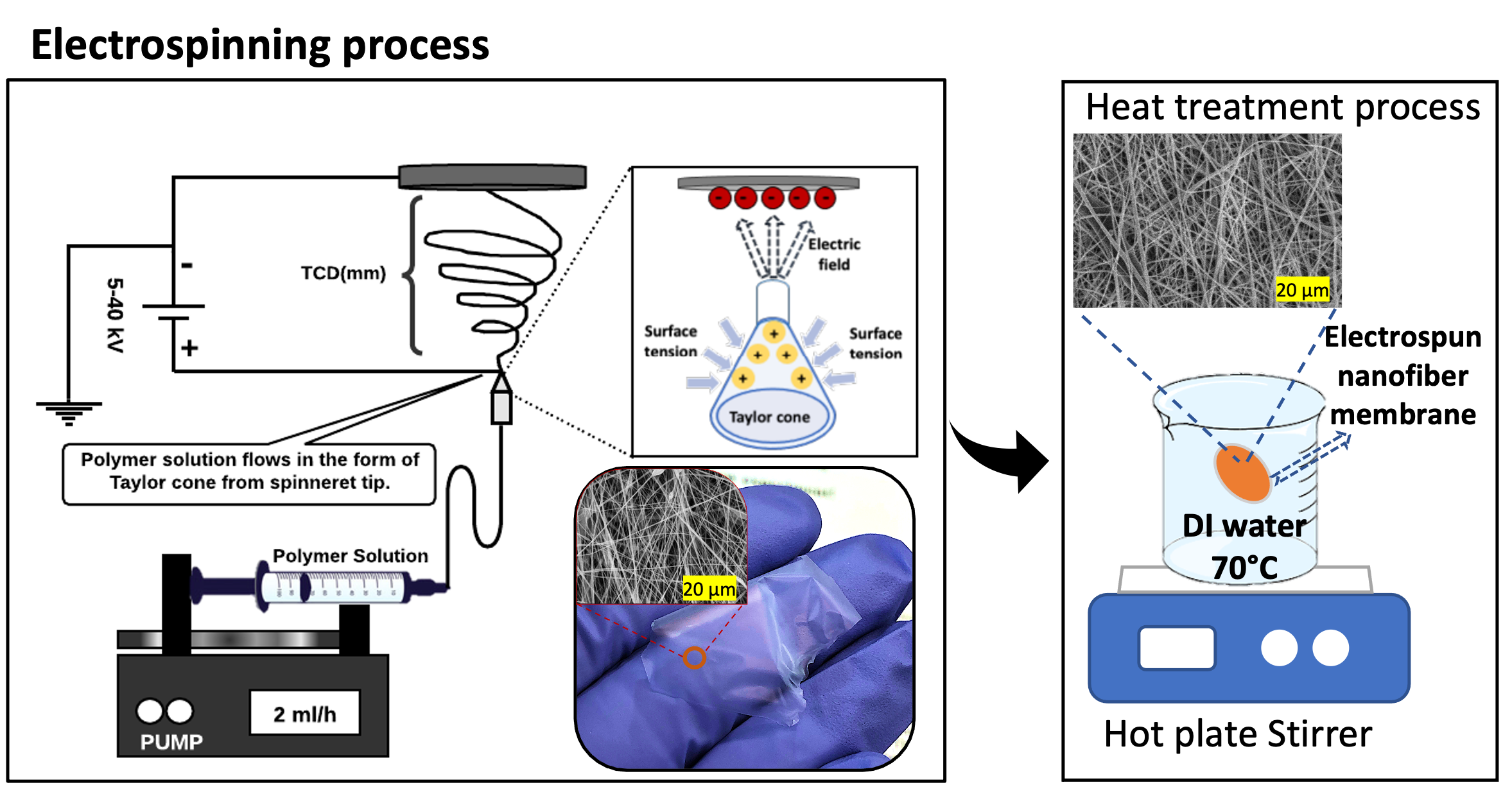
There has been a significant focus on making synthesis techniques more eco-friendly and greener [11], [12]. Figure 1 depicts electrospinning process including heat treatment schematically. Electrospinning offers an incredibly flexible way to produce a wide range of fiber assemblies by fine-tuning polymer solution and electrospinning parameters. In this method, an electrospun nanofibrous membrane (ENM) is fabricated by overcoming surface tension with a polymer solution stretched by electrostatic forces. The electrostatic forces create a uniform nanofibrous membrane with a pore size that can be adjusted by varying the voltage and the concentration of the solution. In this technique, which is based on the electric field between polymer solution droplets in the needle existence and the collector, the conical-shaped droplets are stretched out and form nanofibers collecting on the collector [8], [13], [14].
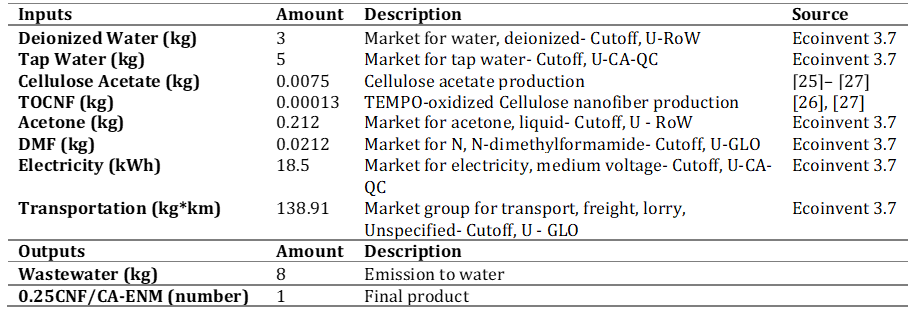
Since membrane technology has developed applications across several markets, for sustaining the growth of the membrane industry, it is critical that we understand how much environmental impact each fabrication method will generate and select the more sustainable and greener membrane fabrication process accordingly. To better assess sustainability in membrane production, it is critical to quantitatively evaluate the impact of the entire process from different perspectives, i.e., global warming, human carcinogenic toxicity, human non-carcinogenic toxicity, fossil resource scarcity, and marine ecotoxicity by Life Cycle Assessment (LCA) approach [15]–[16]. LCA is an analytical and well-established environmental assessment tool to evaluate the cumulative environmental impacts of a product, process, or human activity to derive improvement actions, to develop the products and processes, and to help the decision makers [17]–[20]. Several LCA studies on polymer membranes are available in the literature, with many of them focused on membrane processes (i.e., filtration, desalination, water and wastewater treatment technologies) [21]–[23]. On the contrary, to the best of the authors' knowledge, few life cycle assessment studies have addressed the environmental aspects of the membrane fabrication process, and it is likely due to its complexity involving many different chemicals and polymers. The scope of this research focused primarily on the optimized enhancement of mechanical properties of the cellulose acetate nanocomposite membrane and secondary on the evaluation of the environmental impacts. In this study, we aimed to investigate the environmental impacts of electrospinning technique to fabricate cellulose-based nanocomposite fibrous membrane. Consequently, we selected the membrane synthesized through a single-batch electrospinning process of 50 grams of the 0.25TOCNF/CA nano-composite polymer solution as the focal point for our analysis. To substantiate the robustness of our findings, we conducted an uncertainty analysis employing the Monte Carlo analysis feature within the OpenLCA 1.1 software package. Our study provided a thorough assessment of the environmental impacts across all relevant categories stemming from the production of electrospun membranes.
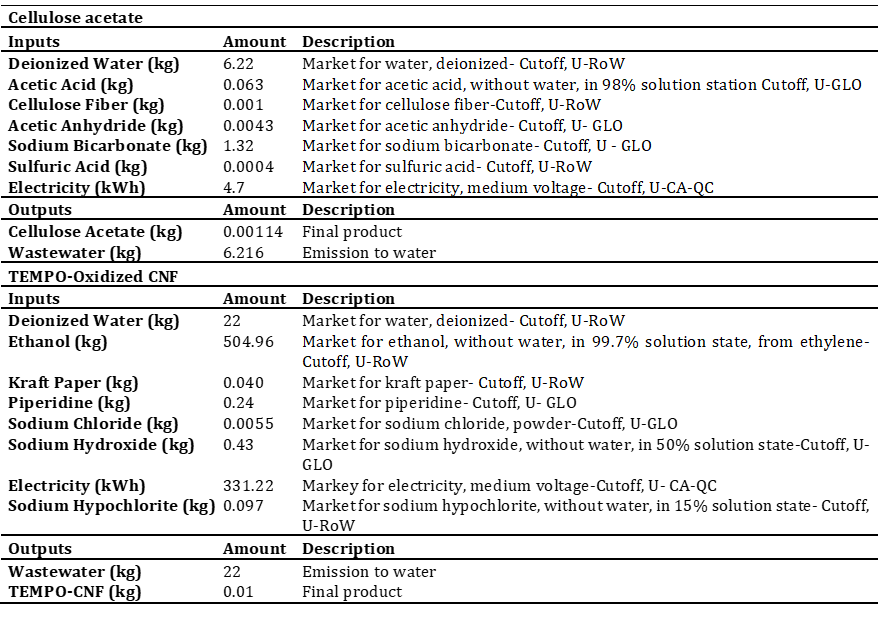
2. Methodology
Subsection 2.1 explains the preparation of nanocomposite cellulose acetate (CA) polymer solution and the synthesis of membrane via electrospinning method. Life Cycle Assessment methodology, i.e., the goal and scope definition, system boundaries, life cycle inventory (LCI), life cycle impact assessment (LCIA), and uncertainty analysis follow in subsection 2.2.
2. 1. Membrane Production Process
As part of the preparation of 50 gr of polymer solution composed of 15 wt% CA (7.5 gr) as matrix polymer, and 0.25 wt% 2,2,6,6-tetramethyl-1-piperidinyloxyl (TEMPO)-oxidized cellulose nanofiber (TOCNF) (0.125 gr) as reinforcing agent were dissolved homogeneously in 22.44 mL Dimethylformamide (DMF), and 26.79 mL acetone as the mixture solvent for 24 hours with a magnetic stirrer at 300 rpm, followed by ultrasonication at ambient temperature to achieve a good dispersal of nanofiller. Figure 1 schematically illustrates the electrospinning process for fabricating nanocomposite fibrous membranes. To form the fibers, a BD plastic syringe with a capacity of 20 mL is connected to a spinneret with an inner diameter of 0.8 mm. The produced nanofiber samples are collected using a collector covered with aluminum foil to facilitate the peeling off the membrane from the collector. Moreover, the spinneret and the collector are two electrodes that are driven by a power supply (0-40 kV) in order to form nanofibrous membrane mats by electrostatic force.
2. 2. Life Cycle Assessment Methodology
For investigating the environmental impacts of the membrane fabrication process by electrospinning, LCA provides a standardized method (ISO 14040, ISO 14044). As a final product, the nanocomposite 0.25TOCNF/CA membrane is considered in order to quantify all emissions and resources consumed, as well as the associated environmental and health impacts. Defining the goal and scope, analyzing life cycle inventories, assessing environmental impacts, and interpreting the results are all critical components of an LCA study. Membrane manufacturing models were generated and assessed by OpenLCA version 1.1 software, the Ecoinvent 3.7 database, and the obtained and gathered data from experiments, and literature review. This section covers the scope and goals definition, system boundaries, LCI, LCIA, and uncertainty analysis.
2. 2. 1 Goal and Scope Definition
This LCA study investigated the environmental impacts of 0.25TOCNF/CA electrospun nanofibrous membrane production process. The functional unit (FU) of analysis was one batch of electrospun membrane samples prepared using 50 gr of 0.25TOCNF/CA polymer solution. We evaluated all inputs (materials and energy requirements) and outputs (emissions) on a per-FU basis. Table 1 shows an overview of the materials and energy requirements for electrospinning a batch of 0.25TOCNF/CA nanocomposite membrane sample. Nanocomposite membranes are the focus of the LCA in this work, making it a "cradle-to-gate" analysis. From the extraction of raw materials to the manufacturing of the final product, the system boundary encompasses all processes including all raw materials, energy, utilities (e.g., electricity and water), chemicals, and emissions during each stage. In this study, the environmental impact of the manufacturing of machinery and the equipment used to fabricate nanocomposite membranes was not taken into account. Emissions to water were considered in terms of environmental impacts.
2. 2. 2 Life Cycle Inventory
This LCA utilizes a comprehensive approach, combining data from the Ecoinvent database (Version 3.7), experimental measurements, literature findings, and estimations to construct its life cycle inventory. Table 1 and Table 2 further provide insights on the Life Cycle Inventory based on FUs. The background upstream manufacturing data for electricity, transportation, water, and chemicals are provided using the inventory Ecoinvent database (Version 3.7). Moreover, information on the synthesis process of CA and TOCNF was gathered from literature [24]–[28] and their environmental footprint was evaluated based on Ecoinvent database v3.7 (Table 2). The Ecoinvent database did not include two key reactants in the TOCNF production process. Due to limited information available on TEMPO's environmental impact, it was not included in the inventory. Furthermore, NaBr is not listed in any of the OpenLCA databases, and NaCl was substituted for it to estimate impacts due to their similar production processes and environmental impacts [22]. We also estimated a value from experience for some process data such as the volume of wastewater produced during the washing process. This analysis was conducted with the following assumptions: 1) While membrane fabrication is done by the NIPS method, nitrogen pressure is constant throughout the entire spinning process at 1 bar. 2) The analysis did not take into consideration the wastewater treatment system. 3) As a result of the volatile solvent used in membrane synthesis, air emissions have not been considered in the analysis.
2. 2. 3 Life Cycle Impact assessment
Using the right impact assessment method is crucial to the success of an LCA study. These methods translate inventory amounts into environmental impacts, Using characterization factors. In this study, an impact assessment based on two methods was conducted. As part of the analysis, the IMPACT2002+ method was used to assess environmental impacts, which is a more appropriate method compared to other methods that were not developed in North America [29], [30]. Based on the 15 midpoint impact categories shown in Figure 2, IMPACT2002+ provided an endpoint damage assessment. The fifteen potential impact categories assessed are aquatic acidification potential (AAP; kgSO2 eq.), aquatic ecotoxicity potential (AEP; kg TEG water), aquatic eutrophication potential (AEUP; kg PO4 P-lim), global warming potential (GWP; kg CO2 eq.), ionizing radiation potential (IRP; kBq C-14 eq.), mineral extraction potential (MEP; MJ surplus), human carcinogenic toxicity potential (HCTP; kg C2H3Cl eq.), human non-carcinogenic toxicity potential (HNCTP; kg C2H3Cl eq.), land use potential (LUP; m2org.arable), non-renewable energy potential (NREP; MJ primary), ozone layer depletion potential (OLDP; kg CFC-11 eq.), respiratory inorganics potential (RIP; kg PM2.5 eq.), respiratory organics potential (ROP, kg C2H4 eq.), terrestrial acid/nutri potential (TANP; kg SO2 eq.), terrestrial ecotoxicity potential (TEP; kg TEG soil). Detailed input and output information presented in Table 1 and Table 2. In terms of damage categories (endpoint impacts), midpoint impacts can be divided into four categories: human health (HH), ecosystem quality (EQ), climate change (CC), and resource depletion (RD). As energy consumption is the most common way of quantifying the environmental impact, we used cumulative energy demand (CED; MJ) to measure the energy consumption within the membrane production process.
2. 2. 4 Uncertainty Analysis
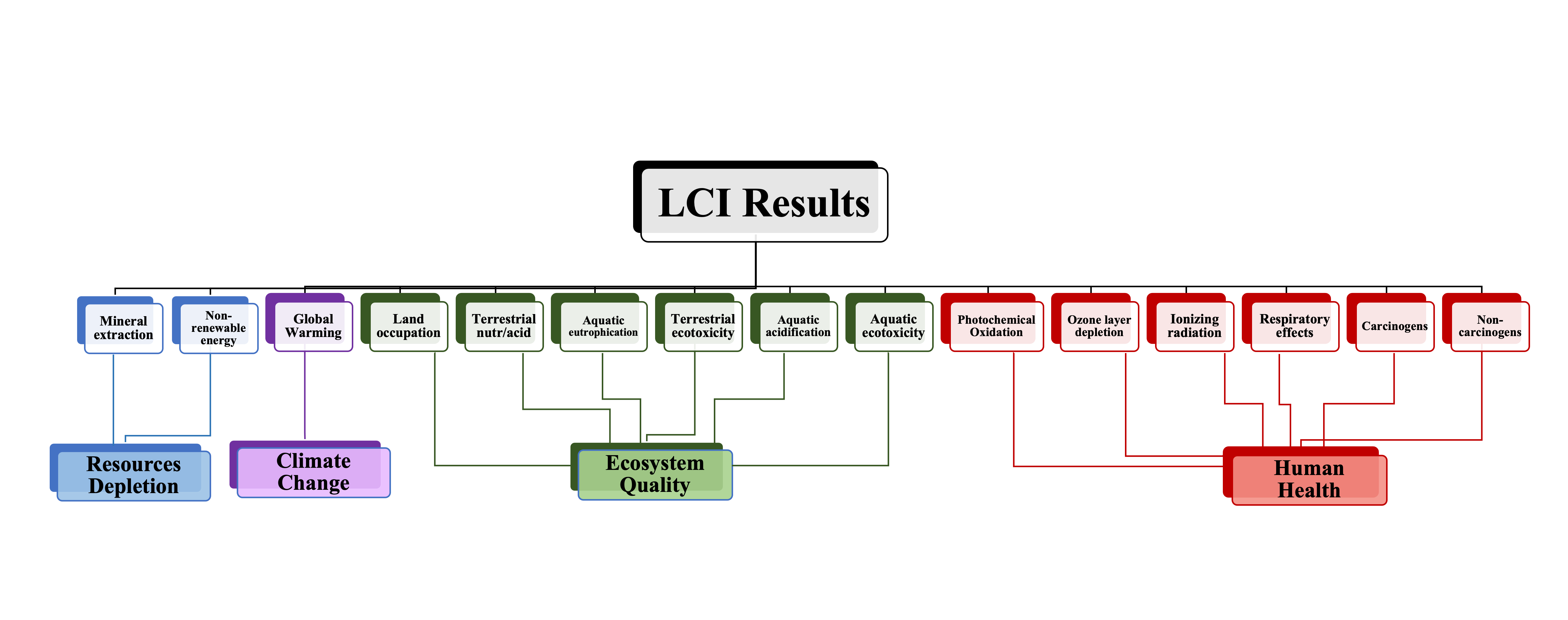
To evaluate the utilized inventory database quality, an uncertainty analysis was carried out for membrane manufacturing. To assess uncertainty, Monte Carlo simulations were conducted using OpenLCA 1.1 software at a 95% confidence level, utilizing inventory data related to the electrospinning of a 50 gr 0.25TOCNF/CA nanocomposite solution. We employed a semi-quantitative approach that relied on the Ecoinvent 3.7 database, wherein we assigned ratings to five data quality indicators: reliability, completeness, temporal correlation, geographical correlation, and further technological correlation. Each indicator was rated on a scale from 1 (highest data quality) to 5 (lowest data quality). To gauge uncertainty in the chosen environmental impact categories, we executed one thousand iterations [31], [32].
3. Results and Discussions
Among the benefits of LCA is the ability to evaluate different scenarios based on different assumptions. By accounting for these scenarios, LCA helps stakeholders understand the impact of their decisions on the environment. An electrospinning approach was used to synthesize 0.25TOCNF/CA nanocomposite membranes and an LCA approach was utilized to assess the environmental impacts of the process. After briefly reviewing the mechanical reinforcement of 0.25TOCNF/CA electrospun cellulose-based membrane sample, this section discusses the environmental impacts of the synthesis method.
3. 1. Electrospun 0.25TOCNF/CA Nanocomposite Membrane Characterization
This study aims to determine the environmental impacts of the fabrication process of 0.25TOCNF/CA membrane that has previously been synthesized and mechanically strengthened [14], [33], [34]. The study was about the mechanical reinforcement of cellulose acetate nanofibrous membranes using cellulose nanomaterials, i.e., TEMPO-Oxidized cellulose nanofibers (TOCNFs) and cellulose nanocrystals (CNCs) and the implementation of heat treatment process. Study results showed that TOCNF exhibited a better reinforcing capability than CNC nanofillers. As a result of heat treatment, the composite 0.25TOCNF/CA nanofibrous membrane sample reached maximum tensile strength of 33.31 MPa and elongation of 1.8% after reaching the breakpoint. Morphological and tensile analyses of the ultimate 0.25TOCNF/CA ENM sample are shown in Figure 3. The fiber diameter distribution and SEM micrographs of 0.25TOCNF/CA nanocomposite membranes as synthesized and after heating are shown in Figure 3-(A), (B). The SEM images reveal an increase in fiber diameter after HPT at constant electrospinning conditions, due to the physical connection between the fibers and a slight melting in the surface of the fibers in the 0.25TOCNF/CA sample. The graph in Figure 3-(B) depicts that at the same nanofiller loading, the fibrous structure of TOCNF causes higher viscosity in the spinning solution resulting in thicker and broader fiber diameter distribution in TOCNF/CA membranes in comparison to CNC/CA samples. The further addition of reinforcing agents results in a more viscous polymer solution. When the viscosity of the solution is higher, at the same electrospinning process conditions, the polymer spinning solution is more resistant to stretching from the electric field force, resulting in thicker fibers. The results of mechanical strength analysis of TOCNF/CA membrane samples are presented in Figure 3-(C). The solid line represents the stress-strain curve of the TOCNF/CA membrane samples before heat treatment, while the dashed line shows the stress-strain curve of the same samples after they were subjected to heat treatment. According to the results, heat treatment strengthened the samples' mechanical properties. Heat-treated 0.25TOCNF/CA membrane samples achieve the maximum ultimate tensile strength (UTS) and fracture strain (dashed blue curve) as compared to unheated samples. The improved mechanical strength and integrity of the membrane sample after heating is attributed to strong fiber connections caused by optimized TOCNF concentration and mean fiber diameter.
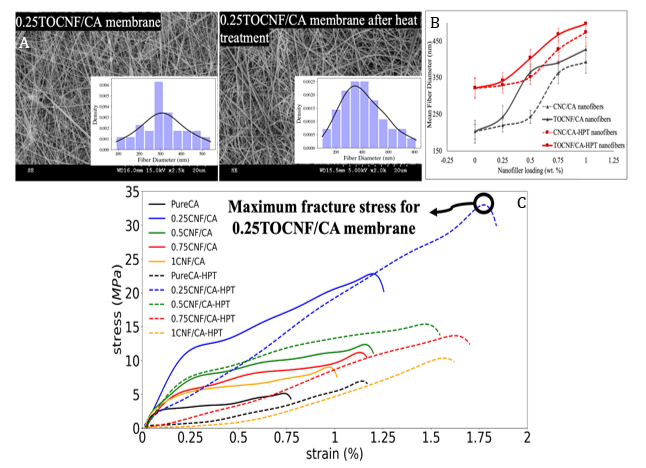
3. 2. Environmental Impacts of Manufacturing Process of Electrospun 0.25TOCNF/CA Nanofibrous Membrane
As mentioned in previous sections, the production process of the 0.25TOCNF/CA electrospun membrane sample is shown in Figure 1. In this section, the environmental impacts of the one batch production of 0.25TOCNF/CA electrospun membrane will be discussed with the consideration of all process steps, applied materials, and energy requirements. The cumulative energy demand for material, electricity, water, and transportation requirement processes of production of 0.25TOCNF/CA ENM sample is shown in Figure 4. According to the pie chart on the right side of the Figure 4, TOCNF, CA, and electricity requirements have greater energy demand (50%, 38%, and 10% of total energy demand, respectively) than transportation, water, and solvent processes. The total energy consumed for electrospinning of 50 gr of 0.25TOCNF/CA polymeric solution was 768 MJ, in which TOCNF production (382 MJ), CA production (290 MJ), and electricity (80 MJ) contributed the main part of the total consumption. The high energy demand for TOCNF production process is mainly related to non-renewable fossil energy which is consumed in the Ethanol production process. In the case of CA production process, the higher energy demand comes from non-renewable fossil energy and renewable water energy which are used for the sodium bicarbonate production process and hydroelectricity power. Since 94% of electricity generation in Quebec province of Canada comes from hydroelectric resources, renewable water energy sources contribute highly to the total cumulative energy demand. The total energy demand for the production process was also broken down into renewable and non-renewable energy as shown in the pie chart on the left side of Figure 4. Energy demand to produce 0.25TOCNF/CA ENM samples is primarily derived from non-renewable sources, which accounts for 539 MJ which is 70% of the total demand.
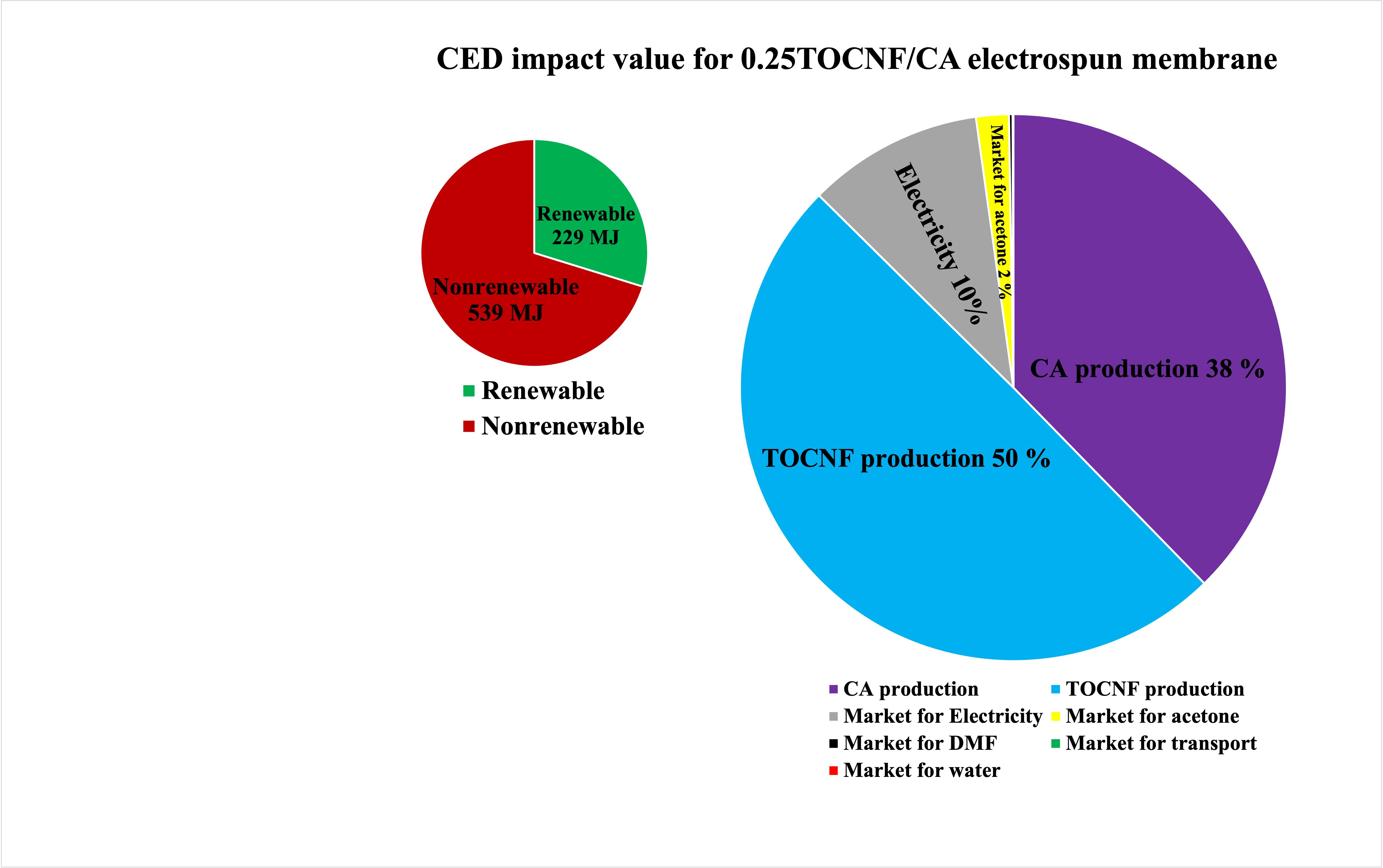
Figure 5 shows the life cycle environmental impacts embedded in the production of 0.25TOCNF/CA ENM. The contribution of materials, electricity, water, and transportation requirement processes to the fifteen mid-point impact categories of the IMPACT2002+ assessment method is shown in Figure 5. The stacked columns indicate that the larger contributions for all mid-point categories come from the CA and TOCNF production processes.
CA production process contributed > 74% and TOCNF production process contributed > 23% of the total aquatic ecotoxicity (AEP) midpoint category in the whole electrospun membrane fabrication process. The major environmental impact of the AEP midpoint category stemmed from soda (> 49%) and DI water (> 10%) used for CA production and ethanol (> 21%) used for TOCNF production processes. The heat production and lime used for soda production and ethylene and heat production for ethanol requirement for CA and TOCNF production were the main responsible for embedded aquatic toxicity impacts. Sodium bicarbonate, electricity, and acetic acid requirements in the CA production process, ethanol consumption in the TOCNF production process, and acetone production process have a far large burden on the global warming (GWP) impact category. Sodium bicarbonate, ethanol, and the other mentioned requirements contributed > 41%, > 43%, and > 10% of the total GWP environmental burden, respectively.
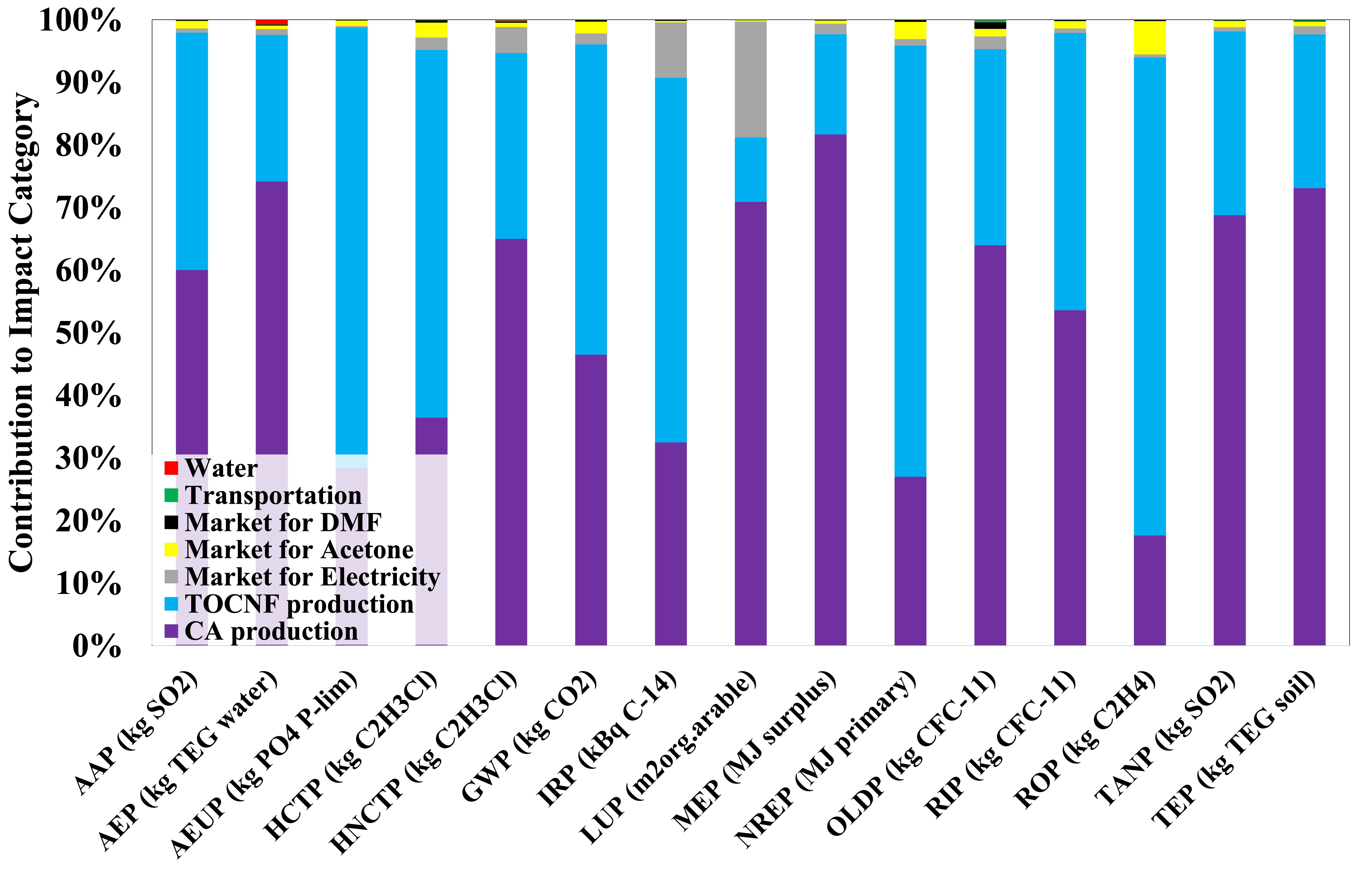
Damage to human health includes midpoint impact categories of carcinogens (HCTP), non-carcinogens (HNCTP), ionizing radiation (IRP), ozone layer depletion (OLDP), and respiratory (RIP and ROP) effects. The use of soda, acetic acid, and ethanol in CA and TOCNF production processes and acetone and electricity consumption dominated embedded carcinogenic and non-carcinogenic toxicity potentials. As can be seen in Figure 5 the dominant contributor in carcinogenic toxicity potential was the TOCNF production process due to ethylene consumption whereas the main risk burden in non-carcinogenic was embedded in CA production because of the soda production process. Moreover, Ethanol consumption highly affected respiratory health impacts by contributing to 76% of risks, and sodium bicarbonate and electricity voltage transformation were responsible for 15% and 79% of ionizing radiation, respectively.
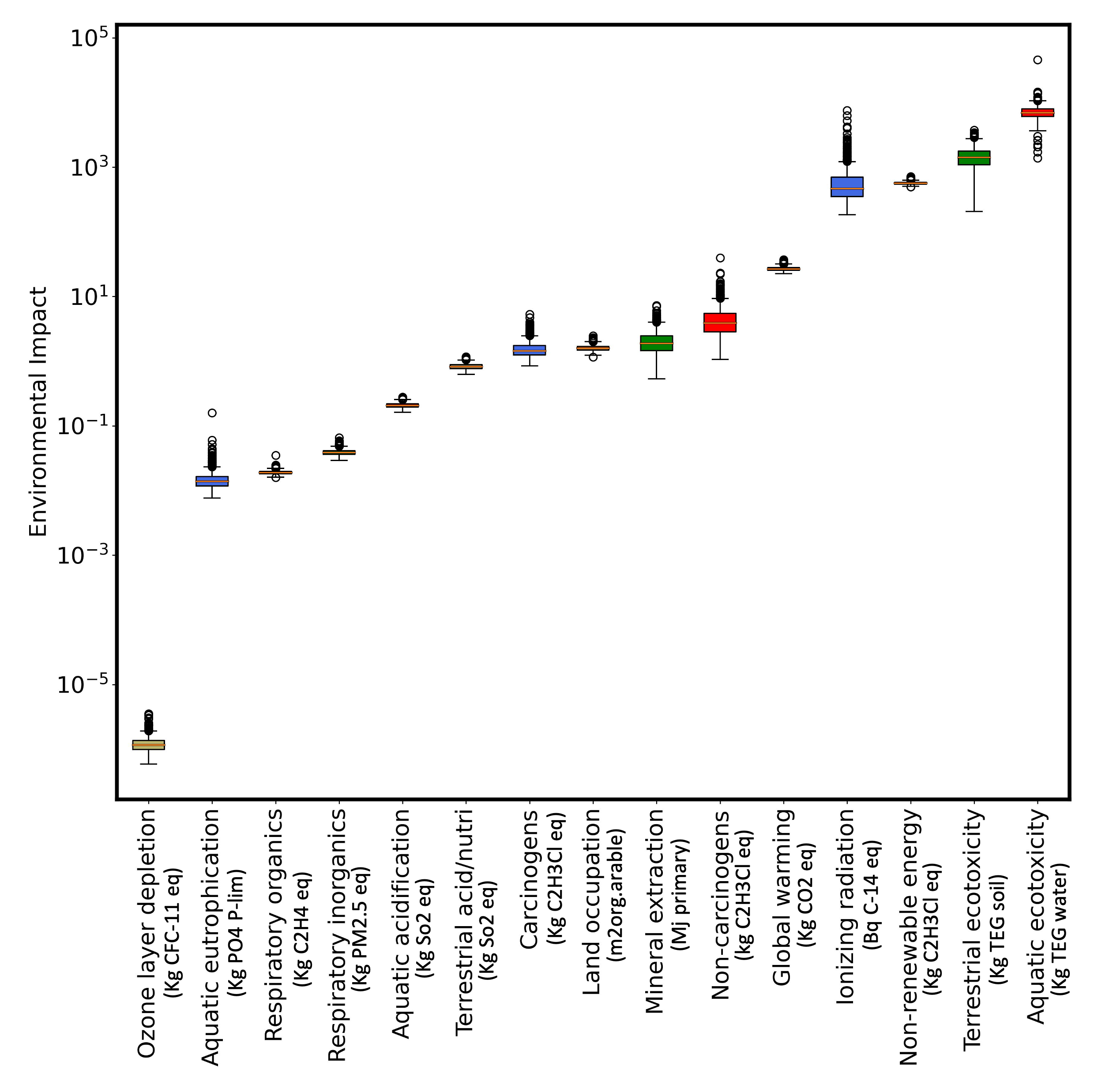
3. 3. Uncertainty Analysis
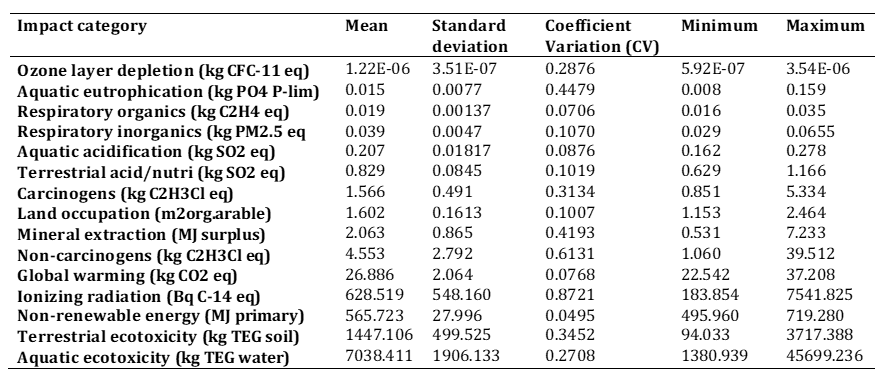
For each environmental impact category, we estimated the coefficient of variation (CV) pertaining to the electrospinning of 50 grams of 0.25TOCNF/CA polymer solution (as shown in Table 3). Lower CV values for the midpoint impact categories imply a higher degree of result reliability with reduced uncertainty. As illustrated in Figure 6 and summarized in Table 3, the analysis reveals that NREP (with a 5% variation), respiratory effects (approximately 8% variation), GWP (7.6% variation), AAP (8.8% variation), and LUP (10% variation) midpoints exhibit the least uncertainty among all the impact categories. Conversely, the higher variation observed in the results for IRP, HCTP, HNCTP, and AEP suggests that these categories carry a greater degree of uncertainty, primarily due to variability issues within the Ecoinvent 3.7 database.
4. Conclusion
In conclusion, this study revealed the environmental impacts of the electrospinning process of 0.25TOCNF/CA nanofibrous membrane sample. By utilizing the Life Cycle Assessment (LCA) approach, it was possible to assess the environmental impacts of each step of the process. Results showed that TEMPO-Oxidized cellulose nanofiber (TOCNF) and cellulose acetate (CA) consumption had a higher environmental impact in terms of midpoint categories related to aquatic ecotoxicity and global warming. Sodium bicarbonate and electricity consumption were two of the primary contributors to global warming and ionizing radiation potentials, respectively. Furthermore, the environmental burden caused by the production of TOCNF and CA were mainly attributed to the consumption of ethylene, ethanol, and acetic acid. This study provides valuable information in terms of environmental impacts of a novel fibrous membrane synthesis technique, i.e., electrospinning. It also provides a better understanding of potential damages to human health, global warming, and ecosystem quality. Additionally, uncertainty analysis assessed the coefficient of variation (CV) for various environmental impact categories during the electrospinning process of 50 grams of the 0.25TOCNF/CA polymer solution, revealing lower CV for GWP, NREP, AAP, LUP midpoints, indicating higher reliability and reduced uncertainty. In the future work, further research is needed to examine the environmental impacts of different nanofibrous membrane production processes and a comparative LCA study should be conducted.
5. Acknowledgement
The authors acknowledge the financial support from École de Technologie Supérieure, Arbour foundation, and Molson foundation.
References
[1] P. Yadav, N. Ismail, M. Essalhi, M. Tysklind, D. Athanassiadis, and N. Tavajohi, "Assessment of the environmental impact of polymeric membrane production," Journal of Membrane Science, vol. 622, p. 118987, 2021. View Article
[2] V. Kugarajah, A.K. Ojha, S. Ranjan, N. Dasgupta, M. Ganespillai "Future applications of electrospun nanofibers in pressure driven water treatment: A brief review and research update," Journal of Environmental Chemical Engineering, vol. 9, no. 2, p. 105107, 2021. View Article
[3] A. G. Fane, R. Wang, and Y. Jia, "Membrane technology: past, present and future," Membrane and desalination technologies, pp. 1-45, 2011. View Article
[4] I. Pinnau and B. D. Freeman, "Formation and modification of polymeric membranes: overview," 2000. View Article
[5] E. M. V. Hoek and V. V. Tarabara, Encyclopedia of membrane science and technology, vol. 3. Wiley Online Library, 2013. View Article
[6] J. Doshi and D. H. Reneker, "Electrospinning process and applications of electrospun fibers," Journal of electrostatics, vol. 35, no. 2-3, pp. 151-160, 1995. View Article
[7] C. Burger, B. S. Hsiao, and B. Chu, "Nanofibrous materials and their applications," Annu. Rev. Mater. Res., vol. 36, pp. 333-368, 2006. View Article
[8] K. Aruchamy, A. Mahto, and S. K. Nataraj, "Electrospun nanofibers, nanocomposites and characterization of art: Insight on establishing fibers as product," Nano-Structures & Nano-Objects, vol. 16, pp. 45-58, 2018. View Article
[9] Z. Zhou, W. Lin, and X.-F. Wu, "Electrospinning ultrathin continuous cellulose acetate fibers for high-flux water filtration," Colloids and Surfaces A: Physicochemical and Engineering Aspects, vol. 494, pp. 21-29, 2016. View Article
[10] Y. Filatov, A. Budyka, and V. Kirichenko, Electrospinning of micro-and nanofibers. Begell House, Inc. Publishers New York, 2007. View Article
[11] F. Prézélus, L. Tiruta-Barna, C. Guigui, and J.-C. Remigy, "A generic process modelling-LCA approach for UF membrane fabrication: Application to cellulose acetate membranes," Journal of Membrane Science, vol. 618, p. 118594, 2021. View Article
[12] J. Kim, "Recent progress on improving the sustainability of membrane fabrication," Journal of Membrane Science and Research, vol. 6, no. 3, pp. 241-250, 2020.
[13] C.-Y. Pan, G.R. Xu, H.L. Zhao, Y.Q. Wu, "Electrospun nanofibrous membranes in membrane distillation: Recent developments and future perspectives," Separation and Purification Technology, vol. 221, pp. 44-63, 2019. View Article
[14] N. Attari and R. Hausler, "Morphological investigation of Cellulose Acetate nanofibrous membranes," in Proceedings of the 4rd International Conference of Recent Trends in Environmental Science and Engineering (RTESE'20), 2020. View Article
[15] G. Szekely, M. F. Jimenez-Solomon, P. Marchetti, J. F. Kim, and A. G. Livingston, "Sustainability assessment of organic solvent nanofiltration: from fabrication to application," Green Chemistry, vol. 16, no. 10, pp. 4440-4473, 2014. View Article
[16] Q. Li, S. McGinnis, A. Wong, and S. Renneckar, "Nanocellulose life cycle assessment," ACS Sustainable Chemistry & Engineering, vol. 1, no. 8, pp. 919-928, 2013. View Article
[17] M. A. Curran, "Life cycle assessment: a review of the methodology and its application to sustainability," Current Opinion in Chemical Engineering, vol. 2, no. 3, pp. 273-277, 2013. View Article
[18] H. Gu, R. Reiner, R. Bergman, and A. Rudie, "LCA study for pilot scale production of cellulose nano crystals (CNC) from wood pulp," in Proceedings of the LCA XV Conference, Vancouver, BC, Canada, 2015, pp. 6-8.
[19] A. Malara, F. Pantò, S. Santangelo, P.L. Antonucci, M. Fiore, "Comparative life cycle assessment of Fe 2 O 3-based fibers as anode materials for sodium-ion batteries," Environment, Development and Sustainability, vol. 23, pp. 6786-6799, 2021. View Article
[20] P. Gallo Stampino, L. Riva, C. Punta, G. Elegir, D. Bussini, and G. Dotelli, "Comparative life cycle assessment of cellulose nanofibres production routes from virgin and recycled raw materials," Molecules, vol. 26, no. 9, p. 2558, 2021. View Article
[21] B. D. Coday, L. Miller-Robbie, E. G. Beaudry, J. Munakata-Marr, and T. Y. Cath, "Life cycle and economic assessments of engineered osmosis and osmotic dilution for desalination of Haynesville shale pit water," Desalination, vol. 369, pp. 188-200, 2015. View Article
[22] P. H. Nakhate, K. K. Moradiya, H. G. Patil, K. V. Marathe, and G. D. Yadav, "Case study on sustainability of textile wastewater treatment plant based on lifecycle assessment approach," Journal of cleaner production, vol. 245, p. 118929, 2020. View Article
[23] N. T. Hancock, N. D. Black, and T. Y. Cath, "A comparative life cycle assessment of hybrid osmotic dilution desalination and established seawater desalination and wastewater reclamation processes," Water research, vol. 46, no. 4, pp. 1145-1154, 2012. View Article
[24] A. Coletti, A. Valerio, and E. Vismara, "Posidonia oceanica as a renewable lignocellulosic biomass for the synthesis of cellulose acetate and glycidyl methacrylate grafted cellulose," Materials, vol. 6, no. 5, pp. 2043-2058, 2013. View Article
[25] G. Rodrigues Filho, D. S. Monteiro, C. d. S. Meireles, R.M. de Assunção, D. A. Cerqueira, "Synthesis and characterization of cellulose acetate produced from recycled newspaper," Carbohydrate Polymers, vol. 73, no. 1, pp. 74-82, 2008. View Article
[26] J. Patiño-Masó, F. Serra-Parareda, Q. Tarrés, P. Mutjé, F. X. Espinach, and M. Delgado-Aguilar, "TEMPO-oxidized cellulose nanofibers: a potential bio-based superabsorbent for diaper production," Nanomaterials, vol. 9, no. 9, p. 1271, 2019. View Article
[27] T. Saito, S. Kimura, Y. Nishiyama, and A. Isogai, "Cellulose nanofibers prepared by TEMPO-mediated oxidation of native cellulose," Biomacromolecules, vol. 8, no. 8, pp. 2485-2491, 2007. View Article
[28] F. Z. BERAICH, M. AROUCH, M. BAKASSE, and H. Nasrellah, "From waste to an ecological material: a new way to value the waste paper".
[29] L. Toffoletto, C. Bulle, J. Godin, C. Reid, and L. Deschênes, "LUCAS-A new LCIA method used for a Canadian-specific context," The International Journal of Life Cycle Assessment, vol. 12, pp. 93-102, 2007. View Article
[30] O. Jolliet, M. Margni, R. Charles, S. Humbert, J. Payet, G. Rebitzer, R. Rosenbaum, "IMPACT 2002+: a new life cycle impact assessment methodology," The international journal of life cycle assessment, vol. 8, pp. 324-330, 2003. View Article
[31] R. Heijungs and M. A. Huijbregts, "A review of approaches to treat uncertainty in LCA," 2004.
[32] T. Grant, "Inclusion of Uncertainty in LCA," Centre for Design at RMIT University, Melbourne, 2009.
[33] N. Attari and R. Hausler, "Reinforcing Effects of Fibrous and Crystalline Nanocelluloses on Cellulose Acetate Membranes," Carbohydrate Polymer Technologies and Applications, p. 100281, 2023. View Article
[34] N. Attari and R. Hausler, "Mechanical characterization of Nanocelluloses/Cellulose acetate composite Nanofibrous membranes," 2022. View Article